A hidden cost opportunity
Energy efficiency through proper lubrication
Energy costs remain persistently high and environmental concerns are paramount. Reasons why businesses are increasingly seeking ways to reduce their energy consumption. One often overlooked solution lies in proper lubrication maintenance - a strategy that can lead to significant energy savings while delivering multiple additional benefits.
The hidden energy cost of friction
Did you know that approximately 20% of global energy consumption goes toward overcoming friction? Studies indicate that energy losses due to friction and wear can be reduced by up to 10% through proper lubrication practices.* For industrial operations, where equipment represents the heart of manufacturing processes, this presents a substantial opportunity for cost reduction.
How proper lubrication drives energy efficiency
Effective lubrication reduces friction between moving parts in machinery, minimizing energy loss through heat generation. This simple principle translates into increased machine efficiency and reduced power consumption. However, achieving optimal results requires careful attention to the following critical factors:
- Lubricant selection: The right lubricant must match specific component requirements, considering factors such as operating speeds, pressures, and environmental conditions. Using a lubricant with incorrect viscosity or temperature tolerance can lead to increased energy consumption and accelerated wear.
- Application frequency: Maintaining the proper lubrication schedule ensures consistent protection. Both under and over-lubrication can be detrimental - insufficient lubrication causes excessive wear, while over-lubrication creates resistance that forces machinery to work harder.
- Quantity control: The amount of lubricant applied is crucial. Excess lubricant can build up, increasing friction and heat generation. Conversely, insufficient quantities leave equipment vulnerable to wear, requiring more energy to perform standard operations.
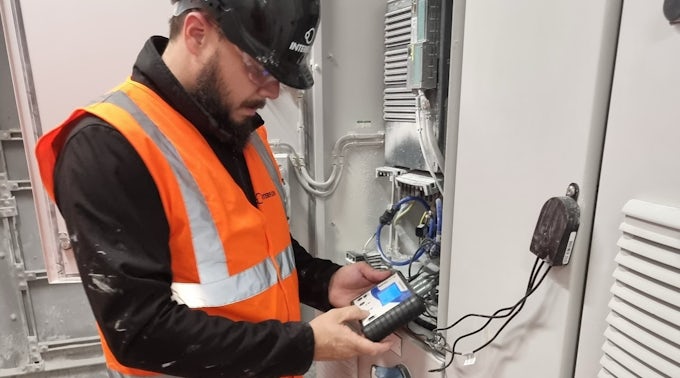
Beyond energy savings: additional benefits
Implementing an effective lubrication strategy delivers multiple advantages:
- Environmental impact: Reduced energy consumption directly translates to lower CO2 emissions and a smaller carbon footprint.
- Supply chain benefits: Better maintenance means fewer replacement parts needed, reducing the overall supply chain environmental impact.
- Cost reduction: Beyond energy savings, proper lubrication leads to reduced maintenance costs and fewer unplanned downtimes.
Best practices for implementation
To maximize the benefits of proper lubrication, consider these recommendations:
- Temperature monitoring: Regular monitoring of operating temperatures ensures lubricants perform within their designed parameters.
- Automatic lubrication systems: Where applicable, automated systems can provide more precise and consistent lubrication, further improving efficiency.
- Professional assessment: Consider working with technical lubrication experts to develop a comprehensive lubrication maintenance program tailored to your specific equipment needs.
The business case for action
In an era of economic uncertainty and rising operational costs, optimizing lubrication maintenance represents a strategic opportunity for businesses. The initial investment in proper lubricants and maintenance procedures typically delivers substantial returns through reduced energy consumption, improved equipment reliability, and lower maintenance costs.
As compliance and environmental considerations become increasingly important, the reduced carbon footprint achieved through proper lubrication can help businesses meet their sustainability goals while improving their bottom line.
Need advice or have questions?
Our technical advisors are here to help. Contact us for tailored advice.
*Source: Holmberg K, Erdemir A. Influence of tribology on global energy consumption, costs and emissions: 263--284 (2017).