Always pre-treat new chains
Logoplaste produces 24/7 thanks to chain treatment from Interflon
Who thinks of a chain drive when consuming Heinz tomato ketchup? Interflon's technical advisors! In the Logoplaste factory - where the bottles in question are produced - a problem was recently resolved that negatively affected the reliable operation of the packaging line. After treatment of the chains, the installation runs smoothly and without disruptions.
Heinz does not produce its plastic bottles for various products itself but outsources this to Logoplaste. A smart move, this way the company is completely unburdened in terms of bottle production and keeping them in stock. Henk Hissink is head of TD at Logoplaste and explains: “We first produce a semi-finished product at our location in Elst. In the next step we heat it again after which we 'inflate' it into a bottle with the correct specifications. The bottles are then packed in pallet size. We have an average of 1 week's production in stock, but the larger models are produced 'just in time' for the customer. To always have sufficient stock for our - only - customer, we work 24/7."
Packaging line challenges
In a large hall, the packaging lines place the bottles on pallets and build up the pallet layers. Three vertically positioned columns, driven by chain drives, are installed for this process. The Technical Services team noticed that the chains in these columns were wearing out relatively quickly. As a result, the chains stretched, leading to misalignments and inaccurate pallet stacking. Only regular maintenance could prevent the wear from increasing to the point where the pallet stack might collapse. Logoplaste naturally wanted to avoid the unplanned downtime and high costs that would entail. However, the chains are located at the top of the columns, making maintenance expensive and time-consuming due to limited accessibility.
The pitfall of new chains
Hissink: "We were already familiar with Interflon through their lubrication solutions, which our supplier MCA uses for the linear bearings. Our Interflon contact visits us about twice a year to consult and provide advice. When we needed to know if it was possible to reduce the chain maintenance frequency without sacrificing quality, we reached out to them."
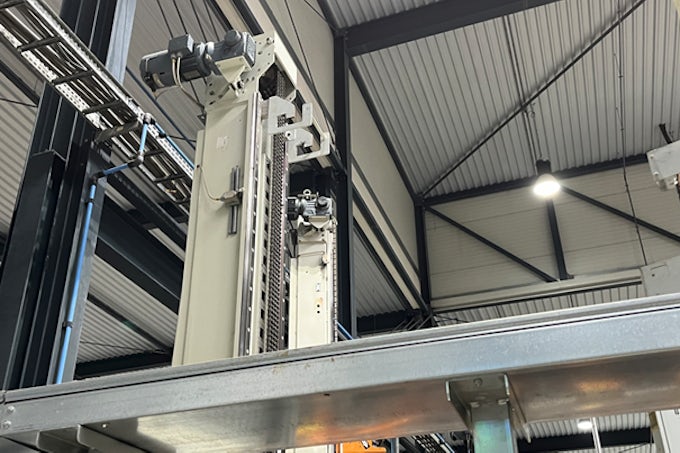
Interflon quickly identified the issue: chains that come straight from the factory are often only treated with a preservative and are not necessarily clean. The risk of residual dirt particles from the production process is high. If these chains are used without treatment, the dirt particles can lead to rapid wear. The solution was clear: the chains needed to be cleaned and treated with a suitable lubricant before use.
The solution
Interflon cleaned and treated the chains at their premises in Roosendaal with Interflon Food Lube G150. The chains were returned to Logoplaste in time and installed during the Christmas shutdown. Since then, the wear issues have been fully resolved.
Hissink adds: "This experience once again confirms the specialist knowledge and expertise of Interflon, which we have benefited from on multiple occasions. We also use the Food Lube aerosol, which allows us to lubricate the chains efficiently and food-safely, and the cleaning product Eco EM100+, which is both human- and environmentally-friendly. It’s a pleasure working with a partner who understands our business and our needs and is always there for us."
Need advice or have questions?
Our technical advisors are here to help. Contact us for tailored advice.