How Hooghoudt keeps its lines clean and its equipment in top condition – with help from ILAC
Clean production, reliable performance
Hooghoudt, based in Groningen, is well known across the Netherlands – and increasingly recognised worldwide – for its young grain jenever, often referred to as Dutch gin. But this family-owned company, founded nearly 140 years ago, also produces syrups, liqueurs, and a wide range of distilled spirits. Inside its production hall, a calm and focused atmosphere prevails as various bottling and packaging lines deliver high-quality end products with great care and precision. That same care extends to the people behind the process – and the machines they depend on. Which is why Hooghoudt relies on Interflon’s ILAC maintenance software to keep operations running smoothly.
Hooghoudt was founded in 1888 by the Hooghoudt couple, who started making syrups and jenever in the basement of their home. Over the years, the range expanded step by step, with a strong focus on product innovation. After relocating several times, the company is now based on Hooghoudtstraat in Groningen. The building has a modern, welcoming interior, including a cosy tasting room for guests. Visitors are guided along a specially designed route that showcases each key stage of the production process. The tour ends on a gallery overlooking the entire production hall.
Flavour, precision and process control
Hooghoudt offers an impressive range of products. The company produces distilled spirits, liqueurs and syrups – each with a wide variety of carefully crafted flavours.

The products are stored in stainless steel tanks and transported via pipelines to the filling, labelling and packaging lines. There, they are bottled or canned, sealed, and – where needed – labelled with precision.
A dedicated pasteurisation line ensures that alcohol-free variants achieve the required shelf life. The products are then automatically packed into boxes, ready for global distribution.
The result is a tightly orchestrated process, where bottles softly clink, conveyor belts glide smoothly, and automation works seamlessly – all contributing to a final product made with care and enjoyed for its taste.
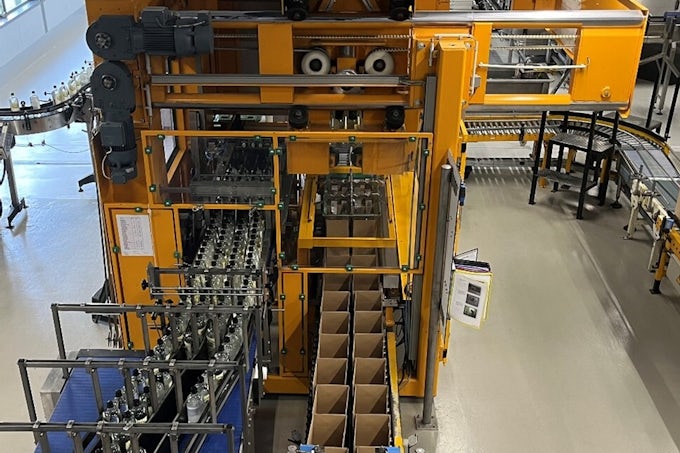
Keeping equipment in peak condition
None of this would be possible without a dedicated maintenance team keeping the production equipment in top condition. Bob Medendorp, Technical Coordinator at Hooghoudt, recalls how he first came into contact with Interflon nearly ten years ago:
“When I started here, ILAC was already in place, but it hadn’t been kept up to date. It was mainly being used as a basic lubrication tool, even though the system has much more potential. Together with Jakob and Albert from Interflon, I put a lot of time and energy into restructuring the platform. We refined the layout and workflows so that ILAC now manages everything – from lubrication schedules to inspections.”
ILAC is a versatile and customisable software platform for maintenance management. Every asset – down to the level of a single lubrication point – can be entered into the system and linked to all relevant data. For lubricants, this includes the type of product, quantity to be applied, and lubrication intervals. The software generates clear maintenance plans and logs all completed tasks and fault reports, building up a reliable maintenance history over time.
Jakob Kooi, technical team member at Hooghoudt, works with ILAC every day:
“The introduction of ILAC brought much more structure – not just for lubrication, but for maintenance as a whole. You can log everything in there, even things like fire safety inspections. At any time, I can generate a list of tasks and when they’re due, which helps me plan monthly schedules. You can also attach useful details – photos, technical manuals, links – so whoever is on the job has everything they need to do it right. Once a task is complete, they check it off or flag any follow-up actions – all directly from their tablet.”
A strong and loyal partnership
Over the years, Hooghoudt’s partnership with Interflon has grown beyond ILAC alone. “As with most of our suppliers, we aim for long-term relationships built on trust,” Bob explains. “You want a partner who’s there when it matters. Interflon has proven to be just that. We’ve had the same contact for years, and he’s always available for questions. If needed, he doesn’t hesitate to get involved himself. I remember a weekend when syrup had spilled onto a conveyor chain. Interflon dismantled the entire chain, cleaned it thoroughly at their own site, and reinstalled it. That kind of support means everything for a company like ours.”
Alongside ILAC and advisory support, Hooghoudt also uses Interflon cleaning products, which are specifically formulated to be safe for both people and the environment – a crucial factor for a company that places high value on employee wellbeing.
Jakob adds: “We’ve installed Single Point Lubricators in a few hard-to-reach spots, but for the most part, our machines get the same attention we give our products and people. Our maintenance technicians rely on all their senses – they hear, see, smell and feel whether an installation is running properly. And when something doesn’t sound right, they know it. That’s something no automatic lubrication system can do. And Interflon understands that.”
The products are stored in stainless steel tanks and transported via pipelines to the filling, labelling and packaging lines. There, they are bottled or canned, sealed, and – where needed – labelled with precision.
A dedicated pasteurisation line ensures that alcohol-free variants achieve the required shelf life.
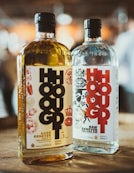