Even if you are not experiencing issues!
Lubrication maintenance: ALWAYS a source of savings
Good lubrication maintenance is an important condition for ensuring reliable, efficient, and safe operation of machinery and equipment. However, 'no malfunctions' does not necessarily mean it is well taken care of. Often, there are still relatively many improvements possible, resulting in cost reductions through longer maintenance intervals, less lubricant usage, and lower energy consumption.
We had an interesting conversation about this with Peter Bakkum, Managing Director of Interflon Holland since three years and advisor to the international industry for over 20 years.

Simple?
The lubrication of machines and machine components has a triple function: 1) reducing friction, 2) dissipating heat, and 3) preserving surfaces. When done insufficiently, it can lead to problems in all three areas. And the consequences are serious.
Numerous studies have been conducted worldwide on the impact of incorrect or insufficient lubrication. Based on these studies, we can state that, on average, 20% of global energy consumption is spent on overcoming friction. This energy consumption can be reduced through good lubrication maintenance.
When looking at maintenance costs, it turns out that only 1-3% of the maintenance budget is spent on lubricants, while incorrect lubrication makes up approximately 15 to 40% of the maintenance costs. This is backed up with data from renowned bearing manufacturers. They have found that approximately half of all cases of premature bearing failure can be attributed to incorrect lubrication maintenance.
No improvement
Peter Bakkum: "This information is not new. The consequences of poor lubrication have been known for years, and research into optimal lubrication maintenance has been conducted for almost as long. Consequently, an enormous amount of knowledge has been developed in the field of tribology, composition of lubricants and additives, as well as regarding the optimal quantity and frequency of lubrication."
"Lubricant manufacturers and suppliers also disseminate this knowledge, but unfortunately, we have to conclude that up till now it has made little difference. The amount of energy required to overcome (excessive) friction remains high. Jammed machine parts and bearing failures due to insufficient lubrication, along with rising operating temperatures, remain a daily occurrence. What is the reason for this?"
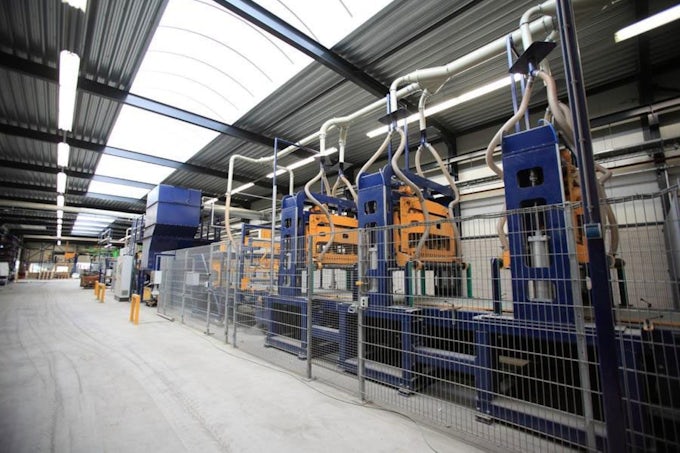
The lubrication maintenance on this tile production line is automated. An improvement to optimize frequency and quantity of lubrication.
A large part of the problems can be attributed to a lack of knowledge. Peter Bakkum: "When I attended the last edition of 'Maintenance Next,' I noticed many solutions were demonstrated relating to 'predictive maintenance.' But when it comes to lubrication maintenance, it would be good to go back to basics: ensuring that your components are properly assembled, well-aligned, and lastly, well-lubricated. Prevention is always better than cure."
Incorrect lubrication
Without the necessary knowledge, good lubrication is not easy, and that is precisely what the practice shows: maintenance services lack sufficient understanding of how a lubricant works, its importance, and how to apply it correctly.
Often, it is simply left to the machine operator, for whom lubrication falls under 'first-line' maintenance. Or it is left to a figurative 'junior' who is sent into the factory with a grease gun during idle hours. Problems can arise from using the wrong lubricant, lubricating too late, lubricating incorrectly, or not lubricating at all. Especially when grease nipples are difficult to access, chances are they will be 'forgotten.'
Peter Bakkum: "When you're engaged in lubrication maintenance almost 24/7, you know that it's almost pointless to keep explaining the costs associated with poor lubrication to some companies. These companies focus solely on production and accept regular downtime, frequent bearing replacements, high energy bills, and high lubricant consumption. They seemingly don't realize that production would be higher if unplanned downtime caused by poor lubrication could be prevented."
Approach
"These are companies that don't consider lubrication maintenance important enough, resulting in unnecessary losses. Scientists at Southampton University have conducted research on production losses. When you extrapolate these figures to the Netherlands, you end up with an almost astronomical waste of 6 billion euros due to significant issues with friction, wear, and lubrication."
Fortunately, there are also companies that recognize their problems and work on improvements in lubrication maintenance. And then there's another group of companies worth addressing, according to Peter Bakkum: those that don't experience malfunctions and lubrication-related problems.
"This sounds strange, but when you delve deeper into the matter, the absence of problems is often the result of a preventive maintenance strategy. This means, for example, replacing bearings much sooner than necessary and not examining the underlying cause of why these bearings reach the end of their lifespan so quickly. In many cases, it's excessive friction and thus poor lubrication."
"Companies could improve this by reorganizing and reframing their maintenance approach. This is what I call 'reframing maintenance.' It may not necessarily reduce malfunctions, but it significantly saves on maintenance and material costs, energy expenses, and also contributes to the reduction of CO2 emissions."
"For example, a new machine requires a new lubricant. When problems arise, you try something different, resulting in a proliferation of lubricants. A specialist can help reduce the number of different brands and types by choosing the same suitable lubricant for different lubrication points. Your logistic costs decrease, you can make larger and thus cheaper purchases, your chances of errors decrease (as you have fewer choices), and the risk of expiration decreases. That's step 1."
In the second step, it's important to select the right lubricant. Bakkum is clear about this: "There are several aspects to consider, and they are nothing more than logical when you look at the original functions of lubricants. First, it's wise to choose a lubricant that minimizes friction. At Interflon, this requirement is translated into a proprietary technology with properties confirmed by various independent testing agencies. Reducing friction is our top priority."
"It's also very interesting to see the practical implications when you replace a much cheaper lubricant that performs poorly in minimizing friction with a better lubricant. In these practical cases, we measure factors such as heat generation, the amount of current drawn by an electric motor from the application, as well as the noise level. The question whether the additional costs of such a lubricant outweigh the benefits and associated savings can almost always be answered 'yes.'"
Future
Peter Bakkum concludes: "Sometimes, I take a figurative step back and look at the world from a distance and how the industry approaches lubrication maintenance. I see that organizations that are taking it seriously, investing in knowledge, appointing someone specifically responsible for all lubrication-related matters, and handling it wisely, benefit in so many ways."
"In a vision interview I gave exactly ten years ago, I discussed the increasing lack of skilled personnel, the importance of condition-based maintenance, and the growing importance of knowledge. Now, ten years later, this has come true to a considerable extent, and I believe it's good for maintenance companies and departments to be aware of the possibilities. So that they can take on the challenge in collaboration with lubricant manufacturers and suppliers, and, together, we contribute a little to improving the world."
This article was written by ing. M.de Wit - Blok. It appeared in Industrial Maintenance on May 16, 2023 and has been translated from Dutch.