Tailor-made for your company
Our Solutions
Reduce maintenance costs, increase machine uptime, improve safety, save energy, lower Total Cost of Ownership are common organizational goals. Easier said than done. Our integrated solutions help you to achieve these goals.
Integrated solutions
Just purchasing the right products for the right applications is not enough to achieve the desired results. It takes more to convert a lubricant into a solution. A good product applied incorrectly will be assessed as a bad product, a waste of efforts. We really offer you solutions. Some facts to consider:
- Maintenance is the no.1 controllable expenditure in a plant
- Incorrect lubrication is the no. 1 cause of machine wear and failure
- There is no greater influence on the state of lubrication than human behaviour
With expertise in a wide range of industries in more than 50 countries, and 40 years of experience as a lubrication partner, Interflon offers you integrated solutions. Our technical advisors, application engineers and lubrication consultants make use of more than 2,400 best lubrication practices to help you move forward, supplemented with training programs, consultancy, lubrication management software and lubrication tools. Combined with our products with MicPol® technology, our solutions help you reach your goals and the highest possible standards in safety, efficiency and emissions.
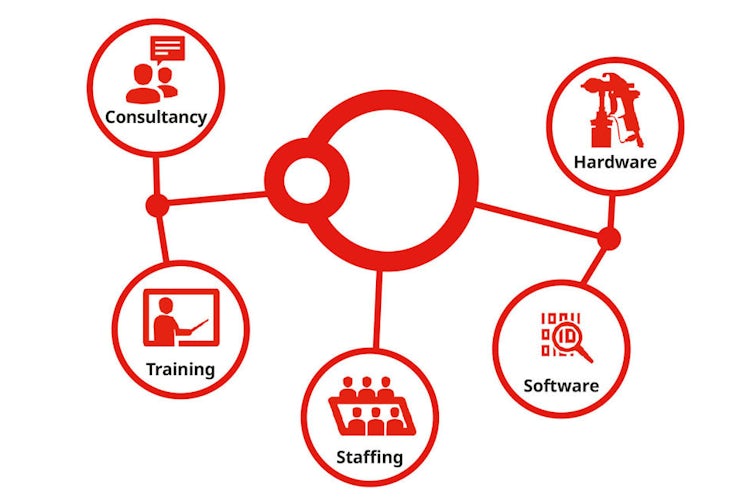
Our approach
As part of our service, our technical advisors follow the next steps:
1) Technical analysis
Together with you we make a technical analysis of the applications to select the right products for your situation. We advise you how, how much and how often they should be applied. It is important that we map your current situation as accurately as possible to be able to evaluate it later.
2) Training of maintenance people
After you have acquired the selected products, we train your maintenance people or machine operators how to use the products. They also receive instructions how to clean properly first.
3) The start up
For all critical applications, but also for other applications if you want, we will be on-site to help you with the first applications to ensure that it is going well. We team up with your people, even if this has to be done in the weekend. We stand next to you.
4) Monitoring and evaluation
After the first application we will visit you frequently to monitor and evaluate the applications and document the results to report back to you. We believe it is important we first gain your trust in our company, our technology and products. Only then you will allow us to focus on more critical machines where the impact of smarter lubrication is greater. We are happy to set up improvement projects with you to demonstrate what our lubricants with MicPol® technology can do for your production process or services.
We can make your machines run better and more efficiently and help you implement methodologies like 6S (previously 5S), TPM and meet quality standards that apply in your organization.