Lubricants that understand your industry
In your business, equipment reliability is key. When the animals are coming in, there are usually dozens of employees ready to process them. Downtime is very costly and can be very stressful for both people and animals.
Your equipment operates under very harsh conditions: heavy loads, daily sanitation with aggressive cleaners and temperature fluctuations. This places high demands on your lubricants to guarantee the reliability of your equipment. Meanwhile, you are not able to stop your production process for maintenance. Lubrication must be therefore quick to apply, reliable and long-lasting.
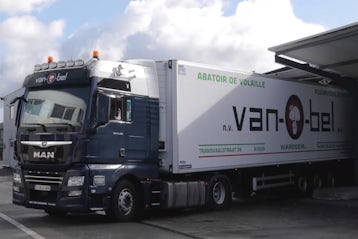
Van-O-Bel
The poultry slaughterhouse Van-O-Bel, founded in 1965, is one of the market leaders in Belgium. The slaughtering capacity has gradually risen up to approximately 900.000 broilers a week. Van-O-Bel has been using Interflon products satisfactorily for years.
Pieter Vanackere, Head responsible Van-O-Bel: "Thanks to Interflon we have extended the lubrication intervals. We have one type of lubricating oil and one type of lubricating grease. It hardly drips off and is therefore a clean lubricant. It ensures efficient management of our machinery and guarantees stability and continuity."
Some examples of applications in poultry
Eliminate dust penetration and rusting issues of your transport chains
The lubricant you currently use on your transport chains is probably one of the many brands of mineral oil with an NSF-H1 certification. However, these traditional lubricants cannot withstand the harsh environment created by daily sanitation involving high-pressure spray guns, hot water and caustic cleaning chemicals. So you are most likely lubricating your chains daily - or at least once a week. Even with this preventative maintenance program, these expensive chains only last one to two years at most plants and they usually suffer from rusting issues as well.
With our NSF H1 certified Interflon Food Lube G-series, you can reduce your oil consumption by 70 or even 90 percent and make your chains last two to four times longer. You will first notice the difference when you no longer have to continuously adjust the chains. Our Food Lube G-series lubricants will virtually eliminate dust penetration and rusting issues. Moreover, there will be no oil dripping onto the birds or the floor. Let’s say you put new chains on your evisceration line and you use Interflon Food Lube G-series. In the past you would have had to make five to six adjustments within the first seven to eight weeks and lubrication would be applied two times a day. Now, in that same timeline, you only need to make two to three adjustments and the Interflon
How dumper chains stay clean and resistant to contamination and rust
Dumpers suffer from dust. Outside they are exposed to freezing temperatures in the winter and hot and humid weather in the summer. The chains on most dumpers cannot be adjusted, so when they start to slap around they must be changed. These chains are lubricated one to even seven times a week, usually with chain oil – not necessarily food-grade oil - from an aerosol can. Even with proper lubrication, contamination builds up on the chains and they rust.
By lubricating with Interflon you can in most cases double the service life of machines. Thanks to our dry MicPol® film, the chains stay cleaner and are extremely resistant to contamination and rust. The highest costs for the conveyor chains are the transfer of the suspension systems. The drive chains rust and stretch in the supply cages, the link chains in the chicken transport. Given the length of the conveyor chains, it is best to lubricate them automatically. Interflon Food Lube AL guarantees a drip-free link chain, an extremely low consumption and a service life of the link chains that can be from 50 to 100% longer.
Reduce grease consumption of bearings by 80 percent
Lubricating with conventional food-grade greases in a poultry plant has its limitations due to sanitation cleaning. The bearings on the machines are exposed to high-pressure sprayers, hot water and harsh cleaning chemicals during the sanitation wash-downs. Maintenance staff then lubricate the bearings in order to purge the water. This results in high grease consumption and labour costs. For example, a Marel Sorter would have to be greased every week on Saturday or Sunday with five to seven pumps per bearing to extract the water.
Thanks to our MicPol® technology, Interflon Food Grease HD2 (NSF-H1) repels water, allowing you to lubricate your bearings once every two weeks with just one or two pumps. This reduces your grease consumption by at least 80 percent. Moreover, your bearing failure rate will drop significantly due to less friction.