Improved uptime and no more peak-season failures by rethinking lubrication approach
From repeated bearing breakdowns to reliable performance
As head of service at Silgan Closures, Felix Hermanns deals daily with the maintenance of machines that apply lids to glass jars – such as those used for preserved vegetables. For a long time, he struggled with a recurring bearing issue in the conveyor units: the prescribed grease was either too thick or too thin and failed to reach all necessary lubrication points, leading to machine breakdowns – sometimes even during peak season. Sometimes even during peak season. Interflon recommended replacing the lubricant with Interflon Food Grease MP2. After a short trial period, the conversion proved successful, marking the beginning of a long-term partnership.
Silgan Closures in Angerlo (NL), is a specialised business unit of the US-based Silgan Holdings. Like its parent company, the Dutch branch supplies metal and plastic lids that fit a variety of jars and bottles for the food and beverage industry. These lids are produced at several locations worldwide. In addition, the company overhauls and maintains the machines at customer sites that apply the lids after the containers have been filled. These machines often operate under demanding conditions, including high temperatures needed to preserve products and ensure proper packaging conditions.
Availability and service
For customers, particularly those processing seasonal produce such as fruit and vegetables, machine reliability and uptime are absolutely critical. Hermanns explains: “Canning companies have to work within tight harvest windows. Produce must be preserved quickly to ensure product quality and shelf life. Machines that handle products like sauces are slightly less time-critical, but still need to operate smoothly and without interruption.”
To maximise uptime, Silgan Closures’ service team performs regular maintenance - typically once a year. This may also include a full overhaul, involving dismantling the drive system and replacing wear parts. A complete overhaul generally takes around three days. Beyond maintenance, Silgan also provides expert advice on process optimisation and product development, making its “total system” offering highly valued across the region.
Persistent bearing problems
Hermanns recalls long-standing issues with the bearings in the conveyor systems. The machines regularly suffered failures due to inadequate lubrication.
"The grease specified by the OEM had a viscosity index that was too low," he explains. "At lower temperatures, it was too thick to reach critical lubrication points, while at higher temperatures, the oil would bleed out of the bearing."
Initially, the team attempted to solve the issue by testing alternative sealing materials, but these efforts only provided limited improvement.
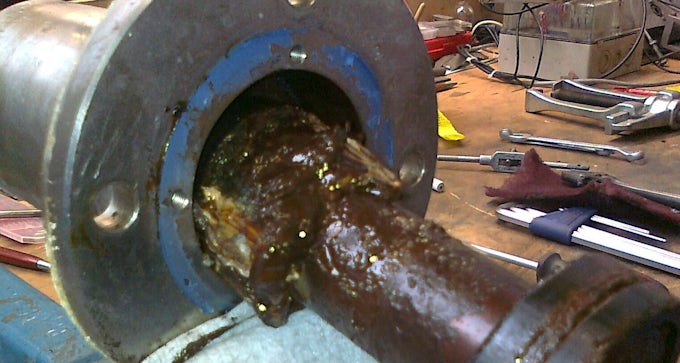
The turning point came when an Interflon Technical Adviser was brought in. The root cause was quickly identified, and a solution proposed: replace the existing lubricant with Interflon Food Grease MP2. This high-performance grease reached all necessary contact points and, thanks to its high viscosity index, maintained a stable lubricating film across a wide temperature range – offering reliable protection even under fluctuating conditions.
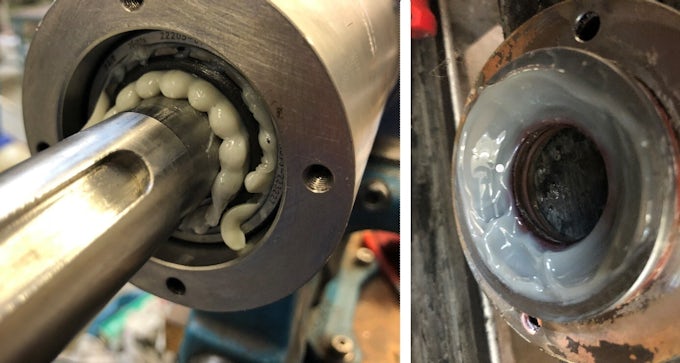
About Interflon Food Grease MP2
MP2 is a high-performance grease based on Interflon’s proprietary MicPol® technology. It is known for its exceptionally long service life and versatility. Suitable for a wide range of mechanical components, including those in food processing equipment, outdoor systems, and vehicles. It operates effectively between -45°C and 150°C (-49°F to 302°F). The grease is resistant to water, steam and contamination, inhibits corrosion. It is NSF H1 listed, making it suitable for incidental food contact – and completely PFAS-free.
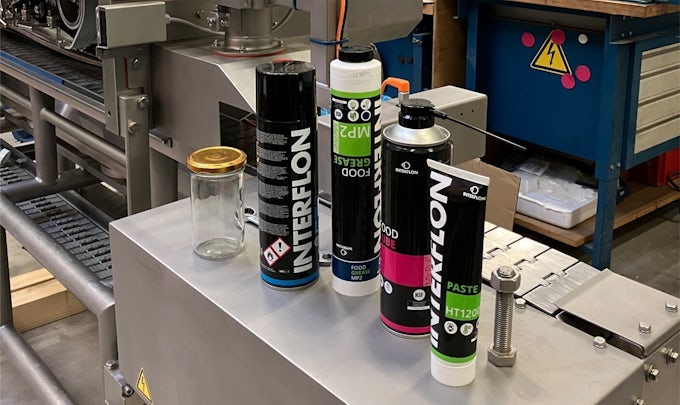
From trial to standard practice
“In 2016, Interflon visited us for the first time,” Hermanns recalls. “We ran initial trials to test their greases under real operating conditions. The results were so positive that we adopted them as standard for every overhaul. The impact has been remarkable. Machines that process acidic products, like pickles and onions, used to fail two or three times a year. Now, they simply receive their scheduled annual service.”
Silgan Closures has since expanded its use of Interflon products, including a high-temperature assembly paste that secures bolted joints and ensures easy disassembly, particularly useful for stainless steel, which can seize over time. The company has also introduced Interflon’s cleaning products into its workshop.
“A great partnership,” Hermanns concludes, “with excellent results thanks to sound advice and first-rate products.”
Do you need expert advice on your lubrication challenges? Get a free, no-obligation consultation today!