Extended bearing life, enhanced reliability and >25% cost savings
Offshore installation crane slewing bearing
Initial situation
The slewing bearing of an offshore installation crane was lubricated with a conventional grease that could not withstand extreme operating conditions. High pressure, humidity, and exposure to a saline environment accelerated grease degradation, increasing friction and leading to premature bearing wear. This significantly raised the risk of unplanned downtime.
Long lead times for spare parts not only result in high costs for labour and materials but can ultimately lead to a complete loss of the crane’s operational availability.
Solution
Following a comprehensive bearing analysis and extensive testing, Interflon Grease LS 1/2 with MicPol® technology was selected as the optimal lubricant for the slewing bearing.
Key benefits:
- Superior adhesion and water resistance, ensuring optimal bearing protection even in harsh marine environments.
- Exceptional high-pressure and load-bearing capacity, minimising wear and micro-pitting.
- Lower coefficient of friction, resulting in improved energy efficiency and reduced thermal load.
- Optimised adhesion and extended service life, reducing lubricant consumption and overall maintenance costs.
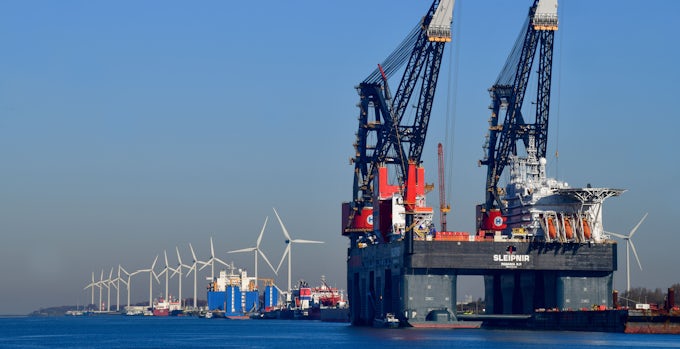
Results
Cost savings
- Reduced lubricant consumption: -26.6%
- Waste disposal costs reduced by 75%
Extended bearing life and reduced downtime
- Significantly lower risk of bearing failure
- Minimized risk of unplanned downtime
- Lower maintenance frequency, enabling more efficient use of labour and resources
Sustainability impact
- 75% reduction in lubricant-related CO₂ emissions, saving 44,687 kg CO₂
- Reduced lubricant waste, lowering environmental impact
- Interflon Grease LS1/2 is fully PFAS-free and complies with the latest environmental regulations
Conclusion
The implementation of Interflon Grease LS1/2 with MicPol® technology has not only resulted in >25% cost savings, but also in a significant reduction in maintenance requirements and enhanced operational reliability.
The extended lubrication intervals and reduced wear directly contribute to a more efficient and sustainable crane operation, leading to less unplanned downtime and lower maintenance costs.