A lubrication story
Maintenance: The true cost
Many of us like to think we have become more responsible as adults, But the simple fact is that many people still make commitments without fully considering the long-term consequences. In the case of business, Industrial lubrication can be a perfect example of this theory. Manufacturing businesses are made up of many individuals who are all tasked with performing the role to the best of their ability. A production manager has the task of ensuring product (the life blood of our business) is manufactured ready to sell. The purchasing manager is focused on business "costs" and ensuring profit is made, in turn securing the future of the business. The Engineering/Maintenance manager has the focus of keeping the business assets running reliably to ensure product can be manufactured. All of this is a circle that when in harmony can result in great things.
But what happens when the circle is not in harmony?
We all get tunnel vision from time to time and human beings tend to focus on what is important to them, often excluding everything else to get to the end goal.
A purchasing managers focus can be solely on "price". The production manager, getting product ready to sell. The engineering manager, working hard within the allotted time to "keep the wheels turning". All doing the job to the best of their ability but not in harmony with each other. In the short term it can look like all are successful in their tasks, Lubrication spend is down, Production is up, Machines are running.
What all 3 individuals share is the inevitable regret that comes when failing to consider the long-term effects of the decisions made.
When working together as a team and effectively communicating each other’s strengths, each area can perform at full efficiency and the results can be outstanding for the business.
The true price you pay for low cost lubricants
Lubricant spend in many cases is one of the first areas where people look to save on "costs" within the business. The old view of "oil is oil" or "grease is grease" is often banded around with little questioning as to "why" there are varying costs to different oils and greases on the market.
What is not understood in many cases is that in terms of "cost savings" within maintenance, lubrication offers potentially the lowest upfront saving but can incur the highest cost to a maintenance budget overall if not taken seriously.
How is this so?
Lubricant spend in general amount to less than 1% of a total maintenance budget, yet lubrication can impact more than 40% of the total maintenance budget in things such as:
- DowntimeFailures
- Replacement parts (Bearings/Chains, Motors etc)
- Increased Maintenance staff costs
- Loss of production
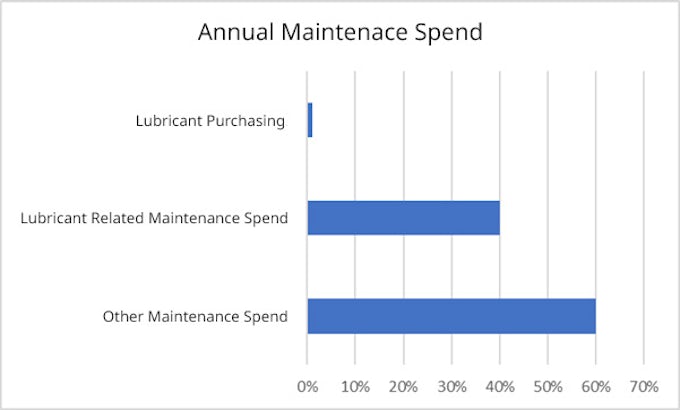
To highlight an example:
A 10% saving in maintenance costs can generally yield a 40% increase in sales turnover
Any increase in Overall Equipment Efficiency (OEE) from your current levels will be pure profit for your company.
If you had a maintenance spend of £100,000 as a company which as we discussed earlier would amount to <1% spent on lubrication, your potential saving on lubrication related products/services is limited to less than £200.
By choosing a more effective lubrication strategy i.e. better performing products, Predictive maintenance strategy, Condition Monitoring, Good lubrication schedules etc. The OEE of your plant can be increased resulting in reduced maintenance spend (up to 40%). This offers a much larger potential saving for your business >40% (£40,000). Imagine getting just 10% of that saving back into your business bottom line.
On another note imagine the adverse effect on bottom line profits a bad lubrication strategy can have or just switching to inferior lubricants just to "save on costs"
Not all lubricants are created the same
There are many lubricants on the market, and all have their place in the correct environment. Lubricants are made up of many different components:
- Base Oils (Mineral/Synthetic)
- Additive Packages (Liquid/Solid, EP etc)
- Soap Thickeners
- Anti-Foam agents
Different lubricants are designed to cope with different operating variants, Additive packages within these are specifically designed for certain applications and have different properties depending on the environment they are performing in i.e. High/Low temperature, High load, Speed variants, Moisture, Chemical Resistance etc. As with everything in life the "cheaper" the lubricant the less quality of base ingredients/additives that are generally added. When deciding on a lubricant supply it is essential that your individual operating environments are considered. Real world applications can be much different to the specification tests performed when the machine was designed.
A "One size fits all" approach to lubricants can be a dangerous road to take when it comes to reliability.
Mixing of lubricants also can introduce issues into a plant maintenance regime as certain oils/thickeners/additive packages don’t mix well and can cause more harm than good.
Lubrication storage and control is a big area that is often overlooked when implementing plant maintenance. Many issues can arise from neglecting this essential part of your maintenance operation such as:
- Lubricant contamination
- Spill hazards
- Cross contamination of lubricants
- Safety of the end user
Lubricants will also have a shelf life and can deteriorate over time when exposed to varying temperatures, UV etc. Good stock management of lubricants is essential to ensure performance is at the highest level when it comes to use, and waste is kept to a minimum. When choosing a lubrication supplier, it is essential you partner with a company who is an expert in this field and can advise you as a company on best practice.
The decision when choosing a lubricant supplier should not just be on "price of product" but on the "cost to the business". When Production, Engineering & Purchasing work together to achieve a world class OEE the results for your business can be outstanding.