Lubrication in high-temperature splicing conveyors
Clean Veneer, Zero Waste, Max Uptime
Initial situation
A Hungarian furniture manufacturer with over 30 years of experience encountered recurring quality issues on their veneer splicing machine. The machine’s conveyor system runs directly next to heating plates, operating at temperatures between 140°C and 210°C depending on the veneer’s thickness and type.
To reduce friction, conventional multi-purpose lubricants were applied to the conveyor pins. However, these products were not suitable for high-temperature use. When exposed to heat, the lubricants would soften or migrate, leading to stains on the finished veneer. In some cases, the veneer had to be discarded due to visible contamination. With veneer costing over HUF 10,000 per square metre (approx. €25.50), even a small amount of scrap meant significant material loss.
Solution
Products used: Interflon Lube TF (aerosol) Interflon Metal Clean F (aerosol)
A structured two-step procedure was implemented:
- Cleaning: The conveyor track and pins were cleaned thoroughly with Interflon Metal Clean F while cold. Compressed air was used to speed up drying.
- Lubrication: A minimal amount of Interflon Lube TF was applied directly to the pins and then carefully wiped with a clean cloth to remove excess.
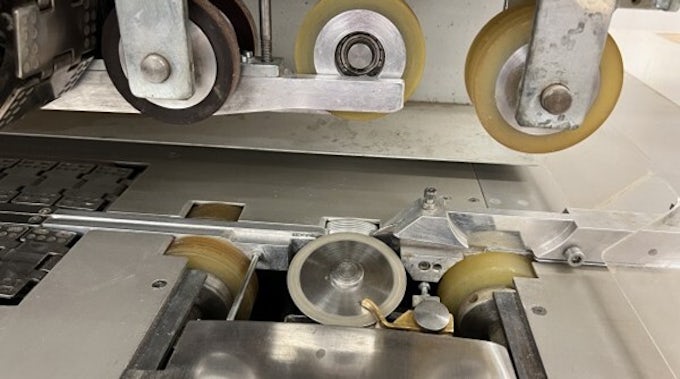
The adhesive is applied here
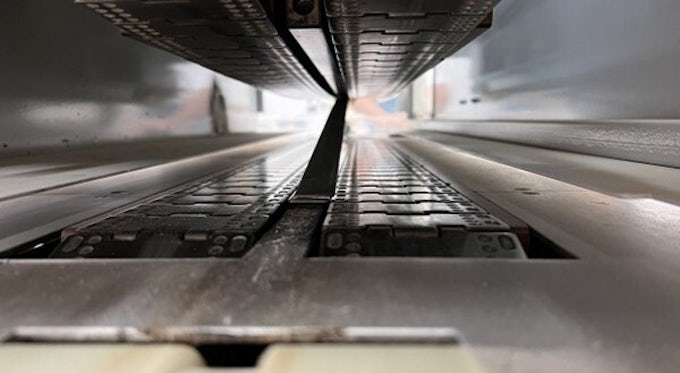
Conveyors lubricated with Interflon Lube TF
Interflon Lube TF, enhanced with MicPol® technology, forms a dry lubricating film that adheres to metal surfaces and resists displacement under thermal stress. Unlike oils and greases, this film does not drip, carbonise or contaminate the surrounding materials – even under continuous exposure to high temperatures.
Results
Since the introduction of Interflon Lube TF:
- No oil stains or residues have been observed on the finished veneer Scrap due to lubricant contamination has been fully eliminated
- Conveyor performance has remained stable and consistent
- Although no exact financial calculation was made, the reduction in product loss, cleaning time, and rework clearly contributed to improved process reliability and product quality.
Conclusion
This case from Hungary highlights the advantages of using dry-film lubrication in heat-intensive environments. Interflon Lube TF, in combination with Metal Clean F, proved to be a technically robust and contamination-free solution for lubricating veneer splicing machine conveyors. By switching from general-purpose lubricants to a heat-resistant dry film, the company was able to protect product integrity, minimise downtime, and reduce waste — all without additional maintenance effort.
For maintenance engineers looking to solve lubrication challenges near high-temperature equipment, this solution offers a proven and cost-effective alternative.