Buffer plates and sleeves
Buffers absorb external forces through buffer plates and dampers. Traditional greases are displaced by high impact, attracting dirt and hardening, resulting in high maintenance and replacement costs. During workshop maintenance, hardened residue must be removed, generating chemical waste disposal expenses. Grease is usually applied manually, resulting in floor contamination and sanitation costs.
Trains are normally not uncoupled during maintenance, preventing grease from reaching the contact surfaces. This causes excessive wear, rust, damper seizing, and noisy buffer heads. This noise creates noise pollution for nearby residents and discomfort for freight workers.
Interflon BufferGuard, specially designed for this purpose, withstands the high impact, shock loads and water wash-off, allowing for longer lubrication intervals. It eliminates dripping, hardening and the need to remove grease chunks, reducing workshop cleaning and chemical waste.
The first time this biodegradable grease is applied, a roller is used to coat the buffer with a thin initial film. Subsequent lubrication can be applied by aerosol, which allows the grease to penetrate more deeply and reach the active contact surfaces without having to uncouple the trains. This also reduces grease waste.
Advantages:
- Remains on the buffer plate, thanks to extreme resistance to pressure and water
- Environmentally friendly, due to biodegradability and noise pollution reduction
- Penetrates between the buffer plates when coupled, making relubrication extremely easy
- Fast and precise lubrication, leading to huge time savings
- No contamination on the floor and no chemical waste
- Can also be used to lubricate tow hook guides and pushers
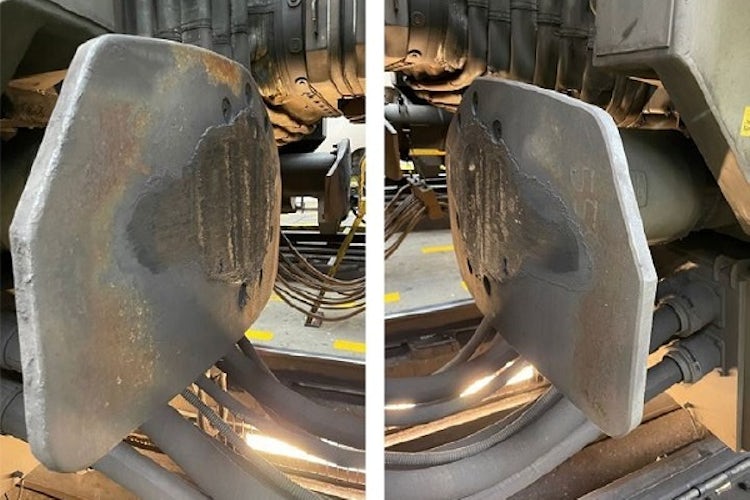