Lubricants designed to resist chemical processes
In a continuous operation, maintenance always works on the limits of their possibilities. Contamination from chemicals, water and particulates and temperature extremes make their task very challenging.
Maintaining equipment for chemical processing and keeping it well lubricated and protected in these harsh conditions, requires another level of lubricants than conventional petrochemical lubricants. Take a look how Interflon lubricants successfully resist these adverse conditions.
Some applications in Chemicals
Dry lubricated chains of the soda packing equipment
In order to avoid dripping, typically these chains are lubricated with a grease. But a grease does not penetrate in the pins and bushes of the chain, promoting premature wear. And the dusty environment makes dust to adhere to the grease, and creates an abrasive paste that has to be cleaned before lubricated again.
Interflon Lube TF is a penetrating oil assuring the lubricant gets into the pins and bushes. Leaves a dry MicPol® that prevents dripping and doesn't allow dust to adhere. It is important to first clean them properly with Interflon Degreaser EM30+ to assure an effective first application. No need to clean before relubrication. Thanks to the solid MicPol® particles, lubrication intervals can be extended by a factor “of” 4 to 8!
Tags: Interflon Lube TF | Interflon Degreaser EM30+ | MicPol®
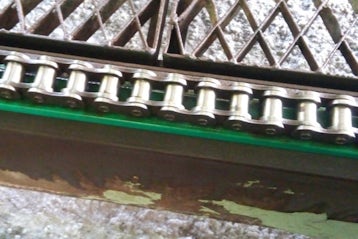
Huge repair cost savings reducer of a palletizer
Because of the continuous start/stop movements of the rapid conveyor belt of palletizers, the drive pinion and the axle suffer high friction that leads to very quick wear of the teeth of the pinion and the axle. More when they work 24/7, 365 days a year. This makes it necessary to dismantle the reducer, and replace the worn parts and gaskets, sometimes every 15 days. In addition, the deterioration of the gaskets causes leaks of the current lubricant.
Interflon Grease MP00, a semi-liquid grease with MicPol®, provides emergency running properties. The MicPol® particles create a solid film that stays adhered on the moving parts of the reducer, avoiding metal-metal contact also when starting up. Service life is extended dramatically. Some customers, although not necessary, replace the parts every 6 months, just for prevention. Huge cost savings, including energy consumption going down due to less friction.
Tags: Interflon Grease MP00 | MicPol®