Maintaining lubricant integrity
7 Preventive strategies to minimize static bleeding
A lubricating grease consists of three elements: the synthetic or mineral base oil (70 – 95%), thickeners (5 – 30%) and additives. The last group gives the grease its specific properties and is always dissolved in the base oil.
When lubricants are at rest (i.e., not in motion or under load), their liquid components can separate from the thickener or additives. Factors such as temperature, thickener type, and base oil viscosity influence this separation. This phenomenon, known as static bleeding, often occurs during storage or prolonged machine downtime. When lubricants 'bleed' they lose part of the base oil. Since the base oil contains the additives, the lubricant will lose an important part of its properties and will no longer be able to fulfill its intended function.
Bleeding is measured as the percentage of oil that separates from the total grease. For most applications, a bleeding rate of 1% to 5% is acceptable, but if it exceeds 10%, it may indicate stability issues in the lubricant. This can lead to severe problems, including increased wear, overheating, higher maintenance costs, and shorter equipment lifespan.
To avoid these issues, it is essential to use high-quality lubricants, select the right product for operating conditions, and follow best maintenance practices.
Strategies to minimize static bleeding in lubrication
1. Choose the right lubricant
Select a lubricant specifically formulated to resist phase separation. Some lubricants include additives that enhance product stability and help prevent static bleeding. Antioxidants, anti-foaming agents, or stabilizers are particularly beneficial in critical operations where lubricants may face significant challenges.
2. Verify thickener quality
Lubricants, especially greases, use thickeners to maintain their consistency. Low-quality or unsuitable thickeners are more likely to cause static bleeding. Using greases with stable thickener systems, such as lithium- or calcium-complex-based thickeners, ensures better resistance to oil separation.
3. Optimise storage conditions
Improper storage can promote static bleeding. Extreme temperatures accelerate the separation of oil from grease thickeners, making it vital to store lubricants in cool, dry areas free from significant temperature fluctuations.
4. Avoid contamination
Contamination with water, dust, or other particles can affect lubricant stability and increase the risk of bleeding. Ensure lubrication points and equipment are clean before applying any lubricant.
5. Control machine operating conditions
Temperature, pressure, and mechanical loads can affect lubricant stability. Monitoring these factors and adjusting lubricant selection if operating conditions differ from expectations is crucial to preventing static bleeding.
6. Regularly replace lubricants
Over time, lubricants degrade, increasing the risk of static bleeding. Establishing a maintenance schedule that includes periodic lubricant replacement, especially for critical equipment, is essential for prevention.
7. Test lubricants regularly
Continuous analysis of used lubricants to assess their quality and to check for phase separation enables proactive measures if the lubricant shows signs of degradation or instability.

Which lubricants are best to minimize static bleeding?
To minimize static bleeding, selecting high-quality lubricants with specific characteristics to avoid phase separation is essential. These lubricants resist the leakage of liquid components when at rest. The most effective lubricants for preventing static bleeding include:
Greases with high-stability thickeners
- Lithium-based greases: Common and stable, these greases offer good resistance to oil separation, particularly under normal temperature and pressure conditions.
- Lithium-complex greases: An improvement over conventional lithium greases, these offer better thermal stability and oil separation resistance, making them ideal for more demanding operating conditions.
- Calcium-complex greases: Highly resistant to static bleeding, these greases retain oil effectively even at high temperatures. They also offer excellent water resistance, making them suitable for humid environments.
Lubricants with anti-wear additives and stabilizers
- Lubricants with antioxidant additives: These additives help prevent lubricant degradation, contributing to long-term stability and reducing static bleeding.
- Additives for thickening and stabilisation: Some lubricants contain additives specifically designed to increase oil stability and prevent phase separation, maintaining a homogeneous structure even during long storage periods.
Synthetic lubricants
- Synthetic greases and oils: Lubricants based on polyol esters (POE) or polyalphaolefins (PAO) offer superior thermal and chemical stability compared to mineral lubricants. They resist oxidation and degradation, reducing the risk of static bleeding. Synthetic blends tailored to specific application needs are highly recommended for extreme temperatures or critical equipment.
High-viscosity lubricants
- High-viscosity lubricants: More viscous lubricants are typically more stable and less prone to phase separation. For suitable applications, using a higher viscosity lubricant can effectively prevent static bleeding.
Polymer-based greases
- Greases with polymer thickeners: Polymers used as thickeners in certain greases improve their ability to retain oil and resist bleeding. These greases are highly stable, even under heavy loads or fluctuating temperatures.
Water-resistant greases
- Calcium- or aluminium-soap greases: Especially effective in humid environments, these greases offer high resistance to water and oil separation, reducing the risk of static bleeding.
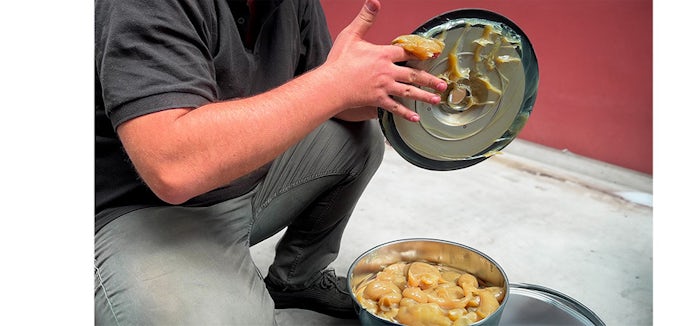
Conclusion
Minimising static bleeding in lubrication requires a combination of best practices in lubricant selection, storage, application, and maintenance. Implementing proper measures to choose the right lubricant and maintain it under optimal conditions can significantly reduce the risk of this phenomenon, thereby prolonging the lifespan of machinery. The key lies in selecting products that provide long-term stability and are formulated to withstand your equipment's specific operating and environmental conditions.