Don't neglect this critical safety step
Wire Rope Lubrication: Ensuring Safety and Durability
Wire ropes, also known as steel cables, play a crucial role in various operations such as lifting, hoisting, towing, dragging and braking. To ensure the safe and efficient functioning of wire ropes, proper lubrication is essential. This article aims to highlight the significance of wire rope lubrication, emphasizing its role in enhancing safety, extending the rope's lifespan, and minimizing the risks associated with wear and corrosion.
Importance of wire rope lubrication
Safety is the paramount concern when it comes to wire rope usage. Improperly lubricated wire ropes are more susceptible to wear, both internally and externally, increasing the risk of failure. A wire rope that breaks during operation can cause severe injuries or even fatalities.
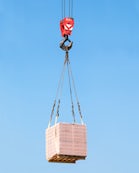
Adequate lubrication acts as a protective measure. It reduces the chances of failure and enhances the safety of workers and equipment involved in lifting and hauling tasks.
Besides that, wire rope lubrication offers economic benefits. A well-maintained and properly lubricated wire rope lasts significantly longer than one that is neglected. By implementing a regular lubrication routine, the service life of a wire rope can be extended several times, leading to substantial cost savings in terms of replacements and repairs.
Lubrication Techniques
To ensure optimal wire rope performance, it is crucial to follow proper lubrication techniques. Similar to any other machinery, wire ropes require thorough cleaning before lubrication. Techniques such as scraping, steaming, or high-pressure washing effectively remove accumulated dirt and grit. Additionally, rust should be regularly eliminated using a wire brush. The cleaning process aims to remove foreign substances and old lubricant from the spaces between strands and wires, allowing the new lubricant to penetrate the rope effectively.
Both internal and external lubrication is necessary to protect wire ropes against wear and corrosion. While exterior wear is more easily identifiable, internal corrosion poses a hidden threat. Visual inspections may not reveal the damage caused by internal corrosion. This makes regular lubrication crucial for preventing unexpected rope failures.
Importance of Inspection
Regular inspections are essential to ensure the ongoing integrity of wire ropes. How often these inspections should take place depends on factors such as rope usage frequency and operating conditions. Abrasion, sharp bends, and reverse bending can cause individual wires to break and bend back. These breaks are known as fishhooks. Always carefully examine wire rope for any signs of fishhooks, kinks, worn spots, or corrosion. Areas where the rope passes over sheaves or onto drums are particularly prone to wire breaks, making them crucial inspection points.
The reduction in the diameter of a wire rope can indicate potential issues such as overloading or insufficient lubrication. If a wire rope reaches 75 percent of its original diameter, it should be immediately removed from service. Pitting and visible corrosion on the rope's surface indicate internal damage, necessitating the rope's replacement.
Take special care to examine the valleys and small spaces between the strands for rust and corrosion. Corrosion is typically caused by insufficient or non-existent lubrication, allowing extreme friction and wear to damage the internal wires. This type of internal destruction is often invisible to the naked eye, making it one of the most frequent causes of unexpected and sudden wire rope failure.
Storage Considerations
Proper storage practices are essential for maintaining the integrity of wire ropes and ensuring their optimal performance. Wire ropes should never be kept in an area where acid is present or has been stored in the past. Even the slightest contact with acid or acid fumes can result in significant damage to the wire rope. It is imperative that wire ropes are stored in a clean and dry environment, away from corrosive substances.
Before placing wire ropes in storage, it is essential to clean and lubricate them properly. Thoroughly removing dirt, grit, and old lubricant from the valleys between the strands and the spaces between the outer wires is crucial. By doing so, you create a clean surface for the new lubricant to penetrate and provide optimal protection against corrosion and wear.
Recommended Wire Rope Lubricants
Choosing the right lubricant is crucial for achieving optimal wire rope performance. Here are some recommendations:
- Interflon Fin Super: Suitable for above-water applications, this spray lubricant provides excellent wear and moisture protection. Its outstanding penetrating and creeping abilities ensure effective lubrication of both the interior and exterior of wire ropes.
- Interflon Lube EP: Formulated to withstand extreme pressure, this lubricant offers similar benefits to Fin Super but is specifically designed for challenging operating conditions.
- Interflon Food Lube: NSF H1 rated and certified kosher and halal, this lubricant is suitable for applications in the food, beverage, pharmaceutical, cosmetic, and animal feed industries. It shares similar properties with Fin Super while meeting stringent industry standards.
- Interflon Fin Grease: This lubricant, available in an aerosol can, expands to a grease upon application, making it ideal for applications that require a more viscous solution.
- Interflon Grease OG: Designed for outdoor and underwater cables, as well as heavily loaded drive mechanisms, this calcium lithium complex grease offers excellent metal adhesion and resistance to washout. Its high temperature range and compatibility with pneumatic lubricant spraying systems make it a versatile choice.
By selecting the appropriate lubricant based on the specific requirements of wire rope applications, you can maximize the rope's performance and durability.
Conclusion
When it comes to wire rope lubrication, prevention is key. By applying proper lubrication techniques, using recommended lubricants, and following best practices for handling and storage, you can ensure the reliability and durability of wire ropes in critical operations. An investment in wire rope lubrication will enhance workplace safety, reduce downtime, and achieve significant cost savings.