Focus on 2025: Reframing Maintenance
Vision for the future
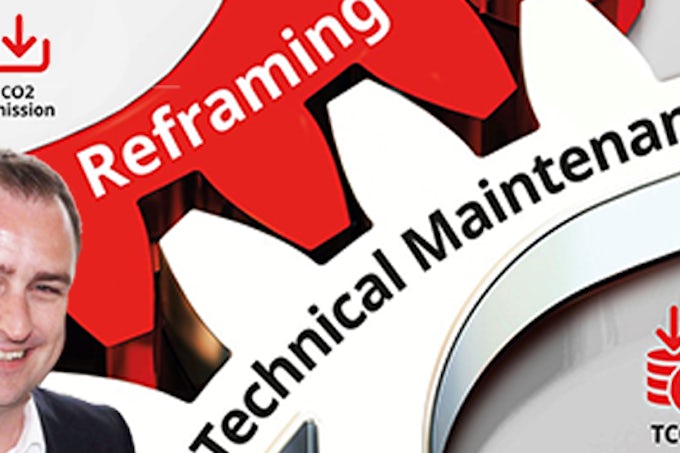
"Friction in machines and installations accounts for 20% of global energy consumption and up to 40% of industrial maintenance costs." With just these two facts, Peter Bakkum, managing director at Interflon Holland, emphasizes the importance of optimal lubrication. By using the right materials and lubricants, energy losses are reduced in the long term by reducing friction by about 25%. A percentage that has an impact on both costs, output and climate.
Peter Bakkum started at Interflon in a more than interesting time. “To begin with, Interflon is ready for the future. As total-solution provider for lubrication problems, we work from a robust basis: a package of high-quality lubricants with excellent properties, including the unique MicPol® technology, production locations that meet the most modern requirements and an optimized logistics system. We have a team of specialists with knowledge of the facts that every lubrication is able to solve the problem. Each and every one of them are people who advise their customers. Our specialists guide them through the implementation of products and processes and can provide training. Where necessary, they can completely unburden customers.'
‘In addition, there are developments outside Interflon that are both worrying and interesting,’ continues Bakkum. "The important in this context is the global climate problem, which is tackled in the Climate Agreement, among other things, by placing the emphasis on CO2 reduction. Most CO2 in the industry is produced by the combustion of fossil fuels. This again is necessary to generate the energy for mainly drives. With the knowledge that 20% of energy consumption worldwide is 'lost' to friction, you understand how important it is to reduce it. Just follow the chain reaction: lower friction, lower energy consumption and ultimately lower CO2 emissions.'
The Importance of lubrication maintenance
Several things are important to reduce friction. First, the basics of a machine or installation must be working properly. That means: the use of components that are tailored to the environment (temperature) and the application (load). In addition, good alignment is essential. When this is okay, the options to further reduce friction are located in good lubrication maintenance.
Peter Bakkum: 'Although there are still enough companies which see maintenance as a final item, and 'greasing' as a task for the youngest servant, you see a turnaround. Companies are taking lubrication maintenance more seriously and are realizing that an integrated, new approach is necessary for various reasons. Certainly not only in the context of CO2 reduction, but also because good lubrication maintenance reduces costs and increases output.'
In concrete figures: a lack of poor lubrication in technical maintenance is responsible for no less than 15% to 40% of the maintenance costs. These are caused by the hours it takes to resolve unexpected downtime – often bearing related – but also by the materials and components that have to be replaced early. Peter Bakkum: 'Finally, insufficient lubrication maintenance leads to production losses due to downtime and shorter maintenance intervals. The latter can in turn be related to the development of heat and wear as a result of friction. In summary: we apply good lubrication maintenance to reduce friction in terms of costs, output and climate.'

Reframing is the solution!
In 2021 Interflon has all the knowledge and resources available to get the most out of lubrication maintenance. Peter Bakkum: ‘Just think about it, we have lubricants with unique MicPol® technology and knowledge of tribology (influence of materials, movements, forces and lubricants on each other). The technical properties of the Interflon MicPol® technology at a very high level, giving our lubricants the lowest possible friction. The next step is now to reframe the maintenance. Or in a Dutch word: to reform.'
Looking into the future, Interflon started supporting companies to reframe their maintenance. ‘It is important to understand that this is a process,’ says Peter Bakkum. "You don't change your entire maintenance in one afternoon. And you don't have to. You can initially focus on the 'low hanging fruit'. First of all to ensure that the basics are in good condition in terms of components (such as bearings) and alignment of the machine or installation.
By then applying the right lubricants in the right place, the friction will (considerably) decrease, as will energy consumption and maintenance requirements. For the longer term, you can also look at the use of materials and components; for example when purchasing a new machine. It is expected that this will reduce the friction by 25% in the long term.”
Convince Business cases
To simplify the transition and raise awareness, Interflon is increasingly working with 'business cases'. Peter Bakkum: “Any company can have this drawn up. Based on knowledge and experience, we make a cost estimate of the old situation and a cost estimate of the situation in which lubrication maintenance is applied correctly. In almost all cases, the business case indicates that significant savings can be made in terms of maintenance, energy consumption, the lubricants themselves and components because they last longer. These savings can add up quickly and quickly justify the investment in better lubricants. Feel free to contact us to make such a business case for your company.'
[1] Bakkum, P, Rondom Interflon voorjaar 2021, Interflon Holland (2021)