3 causes of chain stretch and how to prevent it
3 Causes of Chain Stretch and How to Prevent It
What is chain stretch?
Although chains are frequently described as having stretched due to wear and use, the term “chain stretch” is slightly misleading. The phenomenon of chain stretch is more properly referred to as chain elongation, since it is not the case that the chain links themselves are actually getting longer. In the case of roller chains, it refers to deformation of one or more of the several pieces that make up a chain.
Roller chains are the most commonly-used style of chain in production and assembly environments. They are actually composed of several pieces, as shown in the diagram below:
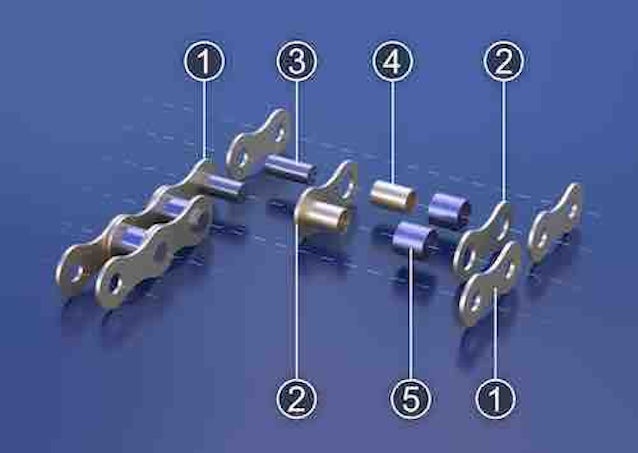
1. Outer plate
2. Inner plate
3. Pin
4. Bushing
5. Roller
The pins (#3) are the part of a chain that are most prone to damage. To be even more precise, these pins are not elongating, but instead are undergoing one of a few possible effects:
- They may be bent to a certain degree
- They may lose material from friction, resulting in a change in their diameter
- There may be a slight widening of the holes in the plates through which pins are inserted.
Over time, the forces of friction, weight, and heat can have multiple harmful effects on the parts of a roller chain.
There are various kinds of roller chains, including single (simplex), double (duplex), and triple (triplex). The more load a chain must transport, the more strands it will contain.
A chain typically is moved by a sprocket, as shown here:
Both chain and sprocket are prone to rapid wear unless properly lubricated.
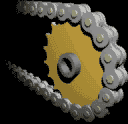
Signs of Chain Stretch
Chances are that you will see signs of chain stretch long before a chain breaks. In fact, breakage is very rare with modern chains. More common is one or more of the following symptoms:
- Excessive rattling, grinding, or other unusual noises coming from the chain drive
- Wear on the teeth of sprockets, often in a characteristic hook shape
- In the case of timing belts, a variation in timing as seen with a timing light
- If a tensioner is being used, the movement of the tensioner can be monitored to see if the required amount of tension has increased
Chain stretch can also be determined through use of the following mathematical formula:
% = ((M-(S*P))/(S*P))*100
Where:
- M is the length of the links measured
- S is the number of links measured
- P is the pitch, or the distance between links
Example calculation:
A chain of 20 links (M) with a pitch of 1 inch (P) measures 20.5 inches (S).
To calculate the percentage of elongation:
((20.5-(20*1))/(20*1)*100 = %
(.5/20)*100 = %
.025*100 = %
2.5%
In this calculation, the percentage of elongation is 2.5%. The chain in this example does not yet have to be replaced, but it's getting close. In this situation, Interflon would recommend regular checking of the chain with a measurement tool until the maximum allowable elongation has been reached.
The most common way to measure chain stretch is through use of a ruler or tape measure. One can also make use of various simple tools that fits into the spaces between pins. Often these will be provided by the manufacturer.
For an example of how chain wear gauges work, and to see different types of chain wear gauges, visit ChainWearGauge.com.
How to Prevent Chain Stretch
The most important factor in preventing chain stretch is lubrication. If roller chains are poorly lubricated, stretching will take place very quickly. When a chain has elongated 3% of its original length, it must be replaced. Replacement is expensive and time-consuming, and necessarily involves shutdowns of production, so obviously a business wants to get as much life out of its chains as possible.
This is where Interflon excels. We save businesses time and money by providing them with high-quality lubricants specifically formulated to prolong the life of chains, as well as other types of production equipment requiring lubrication. Interflon lubricants last much longer than ordinary petrochemical lubricants, thanks to MicPol®, the unique technology that contains micronized, polarized particles of solid lubricant (PTFE).
Interflon lubricants with MicPol® stay much cleaner than wet lubricants, and will not form an abrasive paste of oil and dirt or rust.
MicPol® particles are less than .03 microns in size, about 1500 times smaller than the diameter of a human hair. This gives our lubricants excellent creeping and penetrating abilities, so they can get into the tiny spaces between pins, rollers, bushings, and plates.
MicPol® particles are also polarized, so they carry a negative charge. This means they can bond to the positive particles on a metal surface. As a result, Interflon lubricants with MicPol® often last up to ten times as long as viscous petrochemical lubricants.
To learn more about MicPol®, see our blog post “What is MicPol®?”
Another highly significant factor in chain stretch is the accumulation of dirt particles between parts of a chain. These particles form a paste with existing petrochemical lubricants, and they will cause pins, rollers, and bushings to lose material rapidly, again resulting in an overall elongation of the whole chain. Interflon products are particularly good at preventing this type of wear, because they create a dry film rather than a viscous layer. Whereas sticky oils and greases only accumulate soil, rust particles, and other types of soil that ultimately form the aforementioned abrasive paste, Interflon products do not accumulate particles at all. Instead, they form a dry layer that gives particles nothing to adhere to. With no abrasive paste, there is no excessive wear, and chain life is prolonged by as much as 50%.
A pragmatic or preventive maintenance regime, rather than a calendar-based replacement system, is the key to getting the most out of your chain. For more on what these terms mean, see our blog post entitled “What is Predictive Maintenance?”
Chain strength
Chain strength is measured in two ways:
- Tensile strength: how much load a chain can bear all at once before breaking
- Fatigue strength: Dependent on quality of chain materials
Proper lubrication technique of new chains
When new chains arrive from the factory, they are often coated in wax or another layer of preservative to protect them during transport. It’s important to note that this layer is not intended to serve as chain lubrication, but is applied only for shipping purposes. Furthermore, if this layer is not removed, it will prevent lubrication from reaching the inner workings of the chain, such as between the pins and bushings, or between the bushings and the links.
To effectively remove this protective layer, Interflon recommends immersing the chain in degreaser for a period of 15 minutes, followed by air-drying with a high-pressure air gun or air hose. Once all degreaser has been removed, lubricate the chain properly according to manufacturer’s recommendations.
Chain quality
Another highly significant factor in chain life is the quality of manufacture. Chains can be made from a variety of materials, including:
- Plain carbon steel
- Steel alloy
- Stainless steel
- Nylon
- Brass
References
https://www.ibtinc.com/how-to-measure-chain-stretch/
https://en.wikipedia.org/wiki/Roller_chain
https://en.wikipedia.org/wiki/American_National_Standards_Institute
https://en.wikipedia.org/wiki/Bicycle_chain
https://www.reliableplant.com/Read/8966/wear-life-roller-chains
http://www.fbchain.com/roller-chain-maintenance/roller-chain-sprocket-wear