High temperatures and cooling water
The process of extruding plastic material goes through a sequence of steps where high temperatures and cooling processe make it difficult for maintenance engineers to maximize up-time.
Keeping bearings and screws well lubricated is challenging due the changes in temperatures and presence of water in the cooling section. Apart from this, when equipment comes in for maintenance, the mechanics typically have tremendous difficulties to loosen the screws. Some of them can break off and create extra downtime.
Some applications in Extrusion
No more seized screws
One of the major issues: screws get stuck with the change in temperature and conventional anti-seize metal-based pastes not always do their job. As a consequence a lot of time is spend in trying to loosen them, causing unnecessary downtime or even breaking them.
Interflon Paste HT1200, a ceramic based anti-seize paste, is inert (does not weld) and supports temperatures up to 1200°C, preventing screws from seizing and saving time and creating up-time.
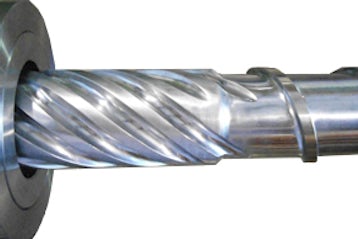

Energy savings on gearboxes
Extruder gearboxes can reach high temperatures and have a negative effect on the properties of the gear oil used, consuming more energy than needed and shortening their service-life.
With Interflon Food Lube G220, a gear oil with MicPol® technology, gearboxes run at the lowest friction possible, considerably reducing temperature and energy consumption (up to 8%). Service-life of the gear oil is typically extended by a factor of 3.