How Interflon contributes to higher efficiency
Supporting new and old textile processing machinery to ensure your assets remain efficient and produce consistent results with a reduction in labour, machine and material waste.
Textiles were the dominant industry of the Industrial Revolution, bringing the inconsistent and unreliable manual weaving from the homes of the workers to the mechanized factory mills. The industry has had to adapt and integrate technology through the ages to fabricate rolls of material efficiently in the harshest of environments and in a cost-effective way.
At Interflon we have a range of proven products (backed up by thousands of proven case studies) that have improved the Overall Equipment Effectiveness of textile machinery working in environments with water, extreme temperatures, demanding unbalanced loads and abrasive textiles fly.
From spinning to finishing, technical textiles to the food compliant confectionary industry we can support you as lubrication partners and work together to provide cost saving solutions.
Some applications in the Textiles Industry
Better protection for your high temperature Tenter/Stenter chain
Stenter/Tenter oven chain is expensive and regularly removed every few years due to contamination from chemical additives in the treatment dip tank which dries hard and create a grinding paste, reducing the life of the chain and need for cleaning. Wet, conventional lubricant can attract abrasive textile fly which results in early failure and can struggle to penetrate to the pins and bushes where the main wear takes place. Wet lubricant can flash off too quickly and relies on re-application for lubrication.
Interflon Lube can be applied both on cold and hot parts (Lube HT / Lube HT/SF, solvent free). The capillary action of the MicPol® technology in Interflon products ensures that the lubricant gets to where it is needed. As the negatively charged and micronized MicPol® is attracted to the positively charged chain, the technology remains in place for longer. Less lubricant is needed than conventional lubrication meaning less waste, less chance of contact with the material (dries clear if contact occurs) and longer time between maintenance intervals.
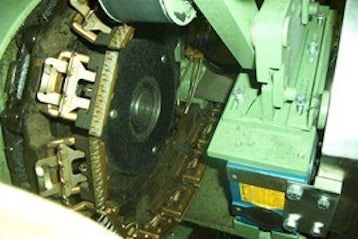