Whitepaper
Man muss etwas tun, um weniger tun zu müssen
Wer täglich 30 Minuten Bewegung bzw. Sport betreibt, wird mit Gesundheit und Vitalität belohnt. Wer etwas an Zeit und Aufwand in die Neugestaltung der Wartung investiert, wird langfristig Zeit, Personalressourcen und Geld sparen. Kurzfristige Mühen werden mit langfristiger Entlastung belohnt – dies ist erwiesen!
Es sind immer wieder dieselben Probleme, die während einer Produktion auftreten und trotzdem wird vielerorts nichts dagegen unternommen. Zum Beispiel wenn man während der Wartung merkt, dass die verwendeten Produkte und Tools nicht optimal auf die Anwendung abgestimmt sind. Oder wenn noch alles manuell gemacht wird und dies zu menschlichem Versagen, also Fehlern führt, die vermieden werden können. Unklare Arbeitsanweisungen und nicht vorhandene Krisenstrategien sind weitere häufig vorkommende Ursachen für Produktionsausfallzeiten. Und trotzdem wird oftmals nichts dagegen unternommen! Die Gewohnheit und auch Angst vor eventuell auftretenden Problemen bei einer Umstellung sind dabei die am häufigsten genannten Gründe.
Restart
Ein Restart ist ein guter Anfang: Von A bis Z die Wartung der Anlagen zu hinterfragen und mit professioneller Unterstützung dort etwas ändern, wo Optimierungspotential dahintersteckt. Das Resultat wird jeden überzeugen: deutlich weniger ungeplante Produktionsstopps und mehr Zeit für andere wichtige Tätigkeiten.
Hier die relevantesten Faktoren für einen erfolgreichen Restart:
- Auswahl des richtigen Schmierstoffs für alle Schmierstellen
- Automatisieren wo geht
- Mehr Zeit in die Reinigung der Teile investieren
- Arbeitsprozesse genau definieren und Mitarbeiter klar anweisen sowie einschulen
Es gibt noch mehr Faktoren und Umsetzungsstrategien, die Sie alle im Whitepaper „Instandhaltung mit geringen Ressourcen“ (s. rechts) nachlesen können.
Fakt ist, dass 45 % an Wartungskosten in einer Produktion von Produktionsstopps verursacht werden. 25 % fallen auf Reparaturen, Instandhaltung und Ersatzteile und nur 5 % macht der Einkaufspreis des Schmierstoffs aus. Selbst qualitativ hochwertigere Produkte machen hier also das Kraut auch nicht fett. Echtes Einsparungspotential steckt in der Reduzierung der ungeplanten Ausfallzeiten, längeren Wartungsintervallen und höherer Lebensdauer der Maschinenkomponenten. Hilfe zur Realisierung dieser Ziele holt man sich am besten in Form von technischen Beratern ins Haus. Sie können gemeinsam mit den Wartungsmitarbeitern Tests durchführen (z.B. Schmierstoffvergleiche an bestimmten Schmieranwendungen) sowie die optimale Auswahl an Produkten für die Reinigung und Schmierung treffen. Zusätzliche Unterstützung bietet Instandhaltungssoftware, die Überblick und Kontrolle über die gesamte zu wartende Maschinenanlage verschafft. Der Weg von einer reaktiven zu einer proaktiven (vorbeugenden) Wartung ist damit geebnet. Eine derartige Software ist auch das optimale Tool zur internen Dokumentation und somit bei Audits das erste Mittel der Wahl.
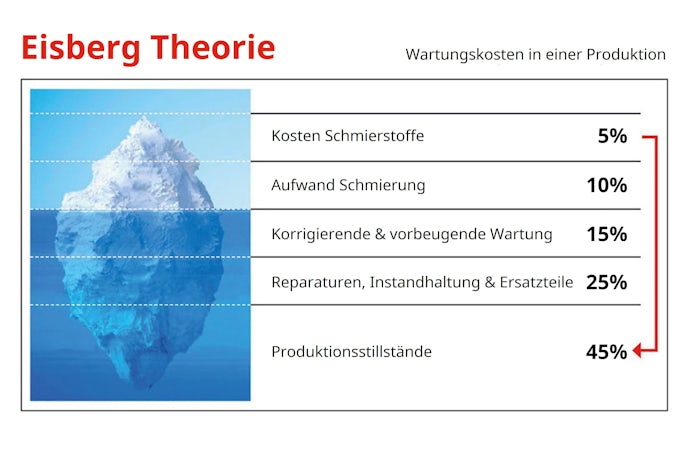
Der Preis für Schmierstoff beträgt nur 5 % der gesamten Wartungskosten, aber die Qualität und die korrekte Anwendung desselbigen hat einen großen Einfluss auf die anderen Kostenkomponenten. 70 % der Wartungskosten bestehen aus Reparaturen, Ersatzteilen und nicht zuletzt unvorhergesehenen und ungeplanten Produktionsstopps. Letztere machen satte 45 % der Gesamtkosten aus!