Lubrication of Belts
Challenge 1: Eliminate the use of water for the lubrication of bottle transport equipment
Initially, the customer used water and detergent to lubricate the conveyor belts. This not only consumed 4,000 litres of water and 200 litres of detergent per month, but also generated waste, bacteria, and wet the floors.
Our solution
We recommended applying our dry-film lubricant Interflon Food Lube AL through automatic lubrication.
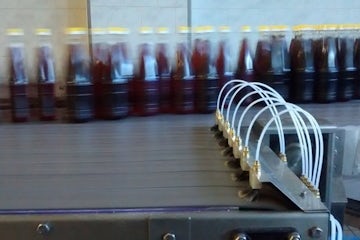
The result
Thanks to Interflon, the following was achieved:
- Elimination of the use of potable water for lubrication, saving 4,000 liters per month
- Extended lifespan of the belts by reducing wear
- Prevention of residue and bacteria formation from water
- Improved plant safety by eliminating water on floors
Challenge 2: Improve product sliding
Bottles were getting stuck on the conveyor belt due to friction between the bottles and the sides of the conveyor belt. This caused blockages and stains.
Our solution
We recommended applying Interflon Slide Wax Dry, our long-lasting dry lubricant engineered for smoothening sliding surfaces.
The result
Applying Interflon Slide Wax Dry:
- improved the movement of bottles
- reduced downtime due to line blockages by 10%
- prevented stains on bottles
- reduced contamination with dust