Filling Machines
Lubricating filling machines in the beverage industry is vital as they operate at high speeds, require extreme precision, and high durability of components. Additionally, it is a critical point in terms of food safety, as the packaged product could be exposed to lubricant contamination.
Challenges associated with these conditions range from contamination and premature wear of mechanisms to the need to maintain productivity without interruptions and ensuring safe lubrication operation for the packaged product.
Interflon addresses these challenges by providing lubrication solutions that meet the specific demands of fillers, including the use of lubricants in minimal quantities, to ensure efficient and reliable operation in the beverage industry.
Challenge 1: Extend the life of the center bearings and their seals (O-rings)
Lubrication issues led to premature bearing failures. Additionally, the filling machine had to be stopped for 30/40 minutes daily for lubrication, causing production losses.
Our solution
We recommended centralized lubrication and Interflon Food Grease S1/2.
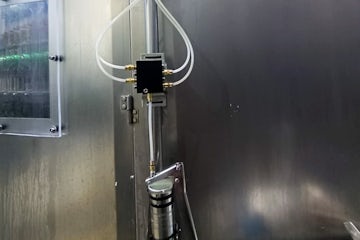
The result
Thanks to Interflon's solution the customer:
- Gained $23,000 a year worth of machine uptime.
- Reduced lubricant consumption by 35%.
- Saved $9,000 a year on lubricant.
Challenge 2: Improve operation, reduce contamination and increase lifespan of open gears
The lubricant used by the customer did not adhere well to the gear, contaminating the floor. Constant relubrication was needed, resulting in high lubricant consumption.
Our solution
We recommended Interflon Food Grease 1.
The result
Switching to Interflon yielded the following results:
- Excellent grease adherence.
- 66% reduction in lubricant consumption.
- 0 grease stains on the floor.
- Increased equipment availability and 80% reduction in labor.
Challenge 3: Prevent contamination and improve valve performance
The PM water valve was lubricated with a multipurpose EP2 industrial grease, unsuitable for beverage production processes. It washed off and contaminated the process water.
Our solution
We recommended Interflon Fin Grease (aerosol).
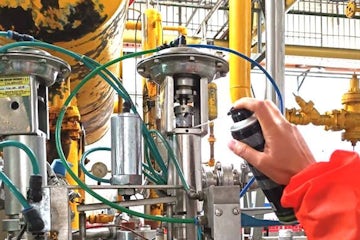
The result
By applying Interflon Fin Grease the customer achieved the following:
- Improved grease adhesion to the valve and improved piston operation.
- 20% reduction in grease loss, extending the lubrication interval.
- Emulsification prevention.
- Enhanced protection of piston and other components.
- Prevention of water and packaged product contamination.