Meeting deadlines whilst reducing maintenance costs and production losses
Within the printing industry effective maintenance is essential to ensure optimum performance of equipment and consistent productivity in order to meet the customer's desired delivery times.
The printing industry faces many production challenges such as paper dust and powder sticking to machine components or mixing with the ink, and grease running out of the bearings and contaminating the printed sheets. These challenges require a strict lubrication and cleaning regime. But due to the deadlines printers must meet to satisfy their customers, this is not always possible, resulting in high maintenance costs.
Some applications in the Printing Industry
Clean and optimal lubricated components
Chains, guides, springs, rods, cylinders, pistons, sealed bearings and grippers suffer from paper dust and antimaculating powder sticking to conventional 'wet' lubricants used to keep a printer running. They create an abrasive paste that is difficult to clean and generates a risk of contaminating the printed sheets.
Interflon Fin Super and Interflon Lube TF provides these components with a dry MicPol® lubrication film, avoiding paper dust and antimaculating powder from sticking to them. The longer lasting effect extends lubrication intervals by a factor 4 or even 6 and reduces the frequency of cleaning, resulting in less production losses and lower maintenance costs.

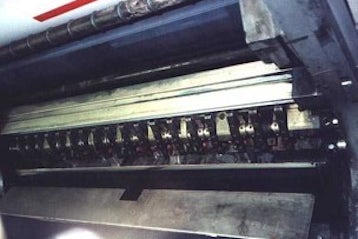
No more grease seeping out of the gripper tongs
Conventional greases seep out of the gripper tongs due to the centrifugal forces and can soil the printed sheets. Frequent lubrication, often once a week, is required to keep them well lubricated causing costly down-time.
Interflon Grease MP2/3
with MicPol® stays within the bearings, eliminating the risk of
contaminating the printed sheets. Greasing intervals can be extended to 6-8 weeks, reducing production losses.