More than just the solution....
A collaboration on a roll
Elevator and escalator manufacturer Schindler discovered Interflon lubricants when service manager Martin Brink was looking for a solution for conditioning certain chains in an outdoor installation of an escalator. With which he not only solved the original problem, but also established an extension of the service life, a lower maintenance requirement, fewer faults and therefore less downtime.
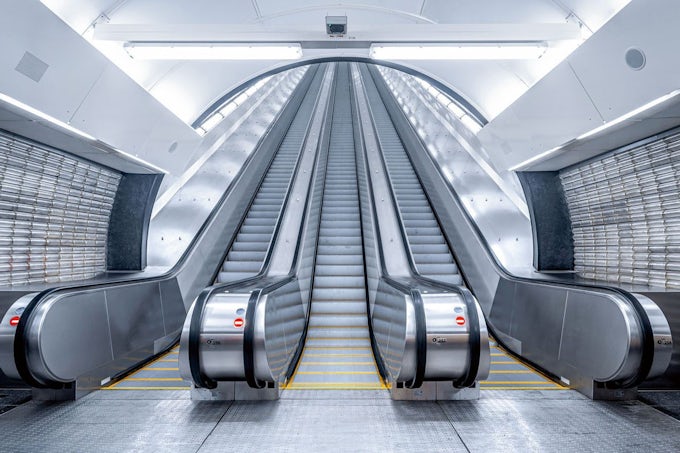
Most people know Schindler from the elevators and escalators you'll find at many locations. Officially escalators and moving walkways belong to the group "machines" and must therefore comply with the associated laws and regulations with regard to safety, among other things. This renowned company therefore pays close attention to the maintenance of these vital components.
Martin Brink is Service Manager of the Escalators sector and says: “We naturally try to maintain our escalators as preventively as possible and to keep corrective maintenance to a minimum. In preventive maintenance, we primarily focus on the safety of the users in the context of limb entrapment. In addition, the adjustments and settings of the chains of the main drive, handrail drive and the step chains of the escalator have our attention. By properly conditioning these, you prevent malfunctions and unplanned downtime or the escalator getting stuck.

Contact Interflon
In principle, Schindler uses the lubricants prescribed by the factory, but these do not always suffice. Sometimes the lubricants give off a specific odor when heated, which is very undesirable in indoor situations and certainly in clothing stores. And there are more situations that can lead to problems.
Martin Brink: “Interflon told us before about the lubrication program and cleaning products. When we encountered a problem with an outdoor escalator at Zwolle station, we decided to try it out. And with success. After a good conversation, Interflon started to work on the chain, which would very quickly add corrosion on the outside.
Another lubricant has been suggested. After that, we treated the chain together on location. How special is it to see the chain being cleaned in front of your own eyes. In no time the escalator was running smoothly again and the breakdowns belonged to the past! Since this success story, this specific lubricant has also been used within Schindler in other outdoor settings.“
Biodegradable
Based on the good cooperation, we also decided to purchase biodegradable lubricants from the Interflon package. Martin Brink says “The nice thing is that these products really penetrate the chains and that there is absolutely no oil leakage during use. That means you don't have to catch it and throw it away. After all, the latter is certainly contrary to the pursuit of an environmentally friendly approach.” Further, Schindler now uses Interflon's Eco degreasers. Cleaning agents with excellent cleaning properties but without harmful gases or propellants, making them safer and healthier to use.
Always new ideas
Martin Brink is very enthusiastic about the collaboration with Interflon. “We are still dependent on the lubricants that the factory prescribes. But if a problem arises, the discussion does not stand long, and we switch. In addition, Interflon regularly comes up with ideas that simplify our lubrication maintenance. Thanks to this proactive thinking, we're working on implementing color codes so that the chance of using an incorrect lubricant is minimal.
Besides, the number of different lubricants has been reduced since the collaboration with Interflon by choosing one suitable product for various products. Of course, this makes the logistics process easier, but entirely for the user. In combination with the color coding, a technician can now easily find the right product off the shelf. In addition, we are currently testing with semi-automatic grease cups that automatically lubricate the steps. Very easy to replace and also a product that makes a good contribution to trouble-free operation. ”

Finally, Martin Brink experiences the service as “excellent”. “When I call I get an answer and if I have a problem, their Technical Advisor drives, even in the evening, to the technician in question for delivering the right product. That means that my customer can use his escalator again already the next day and that's of course means a lot to us. “Moreover, the collaboration is straightforward. If I don't have time, I’ll just say it and Interflon will be back later. Openness. Works great. ”