Reduce el desgaste de tus equipos con sistemas de lubricación automática. Conoce los tipos más eficaces y cómo optimizar el mantenimiento industrial.
Sistemas de lubricación automática: tipos, ventajas y aplicaciones
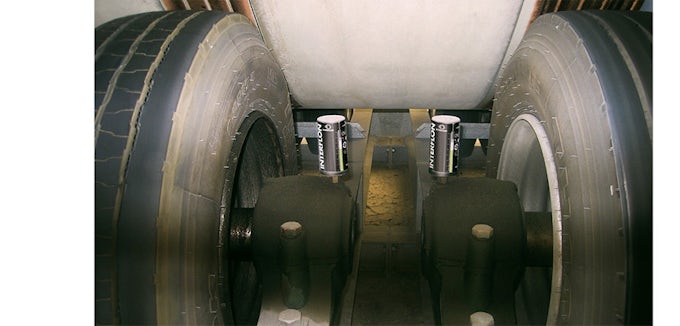
La calidad y adecuación del lubricante son esenciales para llevar a cabo una lubricación efectiva, pero el método de aplicación juega un papel igualmente crucial. La aplicación del lubricante puede realizarse de forma manual o automatizada, y la elección entre ambas depende de diversos factores. Estos factores incluyen el tipo de equipo, las condiciones ambientales de operación, los requisitos de mantenimiento, las especificaciones de la industria y la disponibilidad de recursos. Es fundamental tener en cuenta todos estos aspectos para tomar la decisión más acertada.
Ambas formas son efectivas, pero la lubricación manual puede ser susceptible a una serie de problemas y errores si no se realiza correctamente. Tanto el exceso como la insuficiencia de lubricante pueden afectar al rendimiento y la fiabilidad de las máquinas, lo que requiere una supervisión constante. Por esta razón, en entornos industriales donde se requiere un alto nivel de precisión o donde la aplicación manual presenta dificultades, la lubricación automática se muestra como la opción más eficiente.
¿Qué ventajas aporta la lubricación automática?
La lubricación automática es un método de aplicación de lubricantes que utiliza sistemas automatizados para distribuir de manera precisa y regular el lubricante en los puntos de fricción de los equipos industriales. Estos sistemas están diseñados para proporcionar la cantidad adecuada de lubricante en el momento justo, lo que garantiza una lubricación óptima y continua, minimizando así el desgaste y prolongando la vida útil de los componentes mecánicos. Esto ayuda a mejorar la eficiencia de los equipos y reduce la necesidad de intervenciones manuales frecuentes.
1. Mayor precisión
1.1 La precisión en la dosificación del lubricante puede evitar:
1.1.1 Problemas por exceso de lubricante:
- Fugas: desperdicio de lubricante y contaminación ambiental.
- Sobrecalentamiento: mayor fricción, prematuro deterioro de los componentes.
- Atracción de contaminantes: acumulación de residuos, riesgo de abrasión, mayor desgaste.
- Reducción de eficiencia: Aumento a la resistencia del movimiento, disminución de la eficiencia energética y aumentos de costes.
1.1.2 Problemas por efecto de lubricante:
- Aumento de fricción de las piezas móviles: desgaste prematuro y averías.
- Aumento de la temperatura: deterioro de materiales de los componentes.
- Ruido y vibraciones.
- Corrosión y Oxidación: El aire y la humedad traspasa la barrera protectora y deteriora la maquinaria.
- Perdida de rendimiento: mayor consumo de energía y menor productividad.
1.2 Los puntos críticos exigen una máxima precisión.
Dentro de los equipos y máquinas, existen unas áreas específicas con componentes móviles, donde la lubricación es crucial para su correcto funcionamiento. Estos puntos, están sometidos a una mayor fricción, altas temperaturas o cargas pesadas, e incluso tienen un difícil acceso, por lo que su mantenimiento es más exigente. La lubricación automática es más precisa ante estas problemáticas que la que proporciona una lubricación manual pues garantiza la correcta aplicación del lubricante.
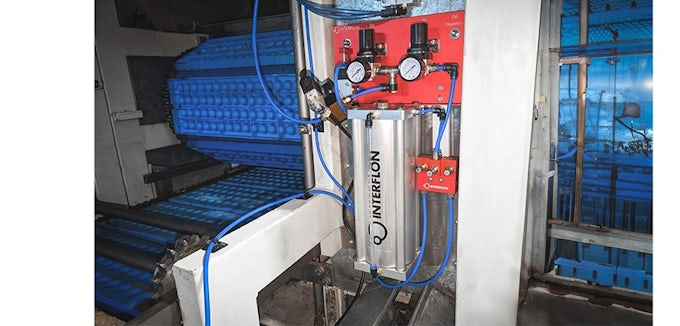
2. Optimiza del uso de lubricantes:
La lubricación automática, al administrar la cantidad exacta del lubricante para cada punto de lubricación, se minimiza el desperdicio de producto, y se reducen, consecuentemente, los costes asociados con la compra y el almacenamiento de lubricantes.
3. Reduce el tiempo de inactividad productiva:
Los sistemas automatizados pueden funcionar mientras la maquinaria está en uso, lo que garantiza una lubricación interrumpida que minimiza el desgaste de los componentes, mejora el rendimiento de los equipos y prolonga su vida útil.
Al automatizar el proceso de lubricación, se reduce la necesidad de detener la producción para realizar las tareas de lubricación manual. Minimizar el tiempo de inactividad no planificado y mantener la productividad de la planta, supone un ahorro en costes de mantenimiento.
4. Supone un ahorro de mano de obra:
Los sistemas de lubricación automática representan una solución eficiente en términos de mano de obra en comparación con la lubricación manual. Al eliminar la necesidad de intervención humana constante, estos sistemas liberan a los técnicos para abordar otras tareas igualmente importantes dentro del ámbito de mantenimiento y operaciones. Esta optimización no solo maximiza la productividad de los recursos humanos, sino que también conlleva una reducción significativa en los costes asociados.
5. Mejora de la seguridad:
Existen puntos de lubricación difíciles de alcanzar, a veces requiriendo incluso la detención del proceso industrial para acceder a ellos, lo que hace indispensable el uso de equipos de seguridad. La lubricación manual puede ser peligrosa en entornos industriales, especialmente cuando se realiza en equipos en funcionamiento o en lugares de difícil acceso. Los sistemas de lubricación automática ayudan a mejorar la seguridad de los técnicos al liberarlos de lubricar en condiciones potencialmente peligrosas.
Los sistemas de la lubricación automática permiten mantener las instalaciones en plena producción, evitando así que los trabajadores se expongan a riesgos al tener que intervenir manualmente.
Además, dependiendo de la industria, el ambiente puede estar contaminado con partículas de polvo, aumentando el riesgo de explosiones, y los vapores tóxicos representan una amenaza constante para la salud de los empleados de mantenimiento. La implementación de sistemas de la lubricación automáticos reduce significativamente la necesidad de manipulación directa de la maquinaria y minimiza la exposición a áreas peligrosas. Esto no solo disminuye el riesgo para los trabajadores, sino que también les proporciona un entorno laboral más seguro y menos expuesto a peligros.
Asimismo, la utilización de engrasadores automáticos puede reducir la necesidad de trabajos en altura con plataformas y arneses de seguridad, que representan un riesgo significativo para la seguridad de los trabajadores.
6. Mejora el Mantenimiento preventivo:
Los sistemas de lubricación automática y centralizada pueden integrarse con sistemas de monitoreo que proporcionaran datos, en tiempo real, sobre la salud y el rendimiento de los equipos. Esto permite una implementación más efectiva de estrategias de mantenimiento preventivo, lo que puede ayudar a prevenir averías costosas y prolongar la vida útil de los equipos. La centralización del sistema también simplifica el mantenimiento, ya que los técnicos pueden supervisar los niveles de lubricación desde un único punto. Con la lubricación automática se reduce el consumo de lubricantes y costes de mantenimiento, al distanciarse las intervenciones provocadas por el desgaste.
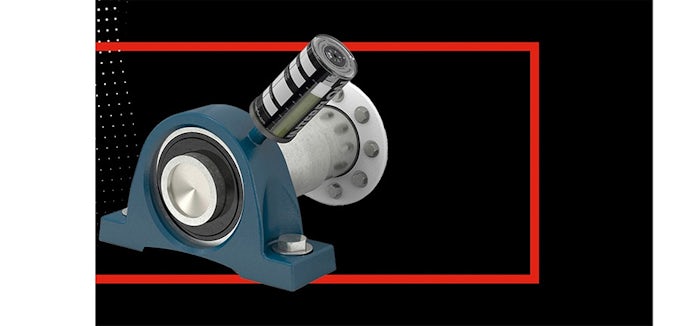
¿Qué tipos de lubricación automática existen y cómo elegirlos?
Existen distintos tipos de sistemas de lubricación automática en función de cómo se distribuye el lubricante. La elección del sistema más adecuado dependerá de las características del equipo a lubricar, con sus correspondientes requisitos específicos de lubricación, y de las condiciones de operativa en las que se trabajará:
Sistema de lubricación por goteo: Este sistema utiliza un depósito de lubricante que suministra lubricante a través de pequeñas tuberías o mangueras a los puntos de lubricación. El lubricante gotea lentamente sobre los componentes en movimiento, proporcionando una lubricación constante y uniforme. Para equipos industriales comunes, como bombas, compresores, motores etc., un sistema de lubricación por goteo puede ser una opción económica y efectiva, que ayuda a reducir el desgaste y prolongar la vida útil de sus componentes.
Sistema de lubricación centralizada: El principio de este método radica en el empleo de una bomba para distribuir de manera automatizada grasa o aceite desde un tanque central hacia los puntos de lubricación. Este sistema garantiza la entrega precisa de las cantidades de lubricante recomendadas por los fabricantes de maquinaria. Cada punto de lubricación recibe la cantidad óptima de lubricante, lo que resulta en una disminución del desgaste. Como resultado, se prolonga significativamente la vida útil de los componentes de la máquina, al tiempo que se reduce el consumo de lubricante. Interflon cuenta con Single Point Lubricator, un lubricador automático monopunto apto para aplicaciones con grasa o aceite para lubricar puntos de engrase de difícil acceso, rodamientos, cadenas o puntos debajo del agua con la cantidad adecuada de lubricante. Además, ofrece Rotalube LC, un sistema de limpieza y lubricación de cadenas que permite aplicar el aceite con precisión directamente a los pasadores de la cadena de rodillos mientras la cadena está funcionando, independientemente de la velocidad a la que trabaje.
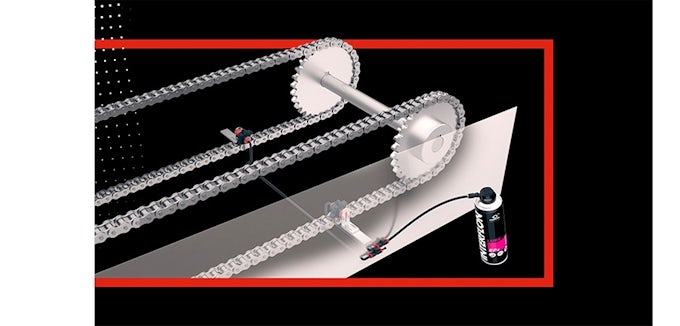
Sistema de lubricación por circulación: En este sistema, el lubricante es bombeado desde un depósito central a través de tuberías o conductos hasta los puntos de lubricación. Después de lubricar los componentes, el lubricante retorna al depósito para ser filtrado y recirculado. Este tipo de sistema es común en aplicaciones donde se requiere una alta precisión en la distribución del lubricante. En máquinas-herramienta como tornos y fresadoras, donde se requiere una lubricación precisa y controlada, un sistema de lubricación por circulación puede ser la mejor opción, pues de asegura la distribución uniforme y la cantidad precisa de lubricante en cada punto crítico.
Sistema de lubricación por pulverización: Este sistema utiliza un pulverizador para rociar el lubricante sobre los componentes en movimiento. El lubricante se atomiza en pequeñas partículas que se adhieren a las superficies de los componentes, proporcionando una lubricación uniforme y eficiente. Este tipo de sistema es especialmente útil en aplicaciones donde los puntos de lubricación son difíciles de alcanzar o están expuestos a condiciones extremas. Así mismo, para el sistema de lubricación por pulverización puede ser más adecuado para equipos que operan en entornos extremos, como altas temperaturas, altas cargas o ambientes corrosivos. Este sistema es el que mejor permite aplicar lubricante de manera precisa y efectiva, incluso en condiciones adversas. Además, Interflon cuenta con Oil Dispenser, un sistema dispensador de aceite que funciona con Interflon Rotalube para lubricar aquellas cadenas en las que no se desea utilizar aerosol y para reemplazar los sistemas de lubricación de cadenas por goteo/cepillos. Es ideal para centralizar la lubricación de varios puntos.
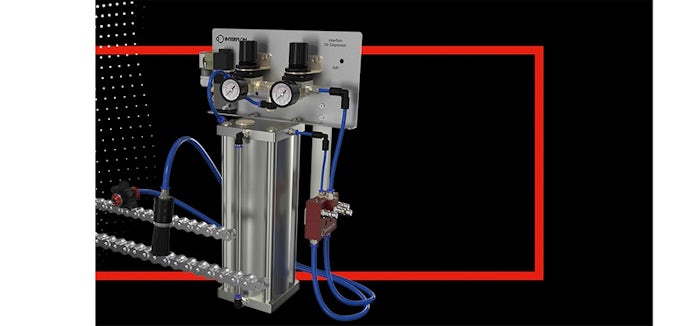
Sistema de lubricación por baño: En este sistema, los componentes están sumergidos en un baño de lubricante. A medida que los componentes se mueven, el lubricante se adhiere a las superficies, proporcionando una lubricación continua. Este tipo de sistema es común en aplicaciones donde se requiere una lubricación constante y uniforme, como en motores y cajas de engranajes. En equipos que operan de forma continua, como compresores y bombas de vacío o cajas de engranajes, un sistema de lubricación por baño puede ser la mejor opción ya que la lubricación constante y uniforme, ayuda a reducir el desgaste y mantener un funcionamiento suave y eficiente.
Sistema de lubricación por aire comprimido: Este sistema utiliza aire comprimido para transportar el lubricante desde un depósito central hasta los puntos de lubricación. El aire comprimido crea una presión que impulsa el lubricante a través de tuberías o conductos hasta los puntos de lubricación. Este tipo de sistema es adecuado para aplicaciones donde se requiere una lubricación precisa y controlada. Este sistema es válido para diversos equipos, pero en especial para aquellos con puntos de lubricación difíciles de alcanzar o inaccesibles, como equipos montados en altura.

Solicita asesoramiento técnico especializado
🔍 ¿Buscas mejorar la fiabilidad de tus equipos, reducir averías o seleccionar el lubricante más adecuado para tus condiciones operativas?
Nuestro equipo de expertos en lubricación te ayudará a identificar la solución óptima para tus aplicaciones, con productos que maximizan el rendimiento y reducen los costes operativos.
📩 Rellena el formulario de contacto y recibe una propuesta técnica adaptada a las necesidades de tu planta o maquinaria.