Optimiza el rendimiento de tu maquinaria con técnicas de mantenimiento predictivo.
IPM (Interflon Predictive Maintenance)
Optimiza tu mantenimiento industrial con Interflon Predictive Maintenance (IPM). Nuestro servicio IPM es la solución definitiva para garantizar el rendimiento y la eficiencia de tus equipos. El mantenimiento predictivo es clave para evitar paradas no planificadas, los tiempos de inactividad y los costes asociados a estos problemas. Con IPM, combinamos tecnologías de vanguardia y técnicas especializadas para brindarte una estrategia completa y proactiva.
Nuestro servicio IPM combina diversas técnicas de mantenimiento predictivo para garantizar un funcionamiento óptimo de tus equipos. Mediante el monitoreo por ultrasonidos, las termografías, las endoscopias industriales y el análisis de lubricantes, ofrecemos un enfoque integral que te ayudará a evitar problemas costosos y maximizar la vida útil de tus máquinas. Nuestros expertos utilizarán estas herramientas para detectar problemas antes de que se conviertan en fallos o roturas costosas, permitiéndote tomar medidas preventivas y planificar el mantenimiento de manera más eficiente.
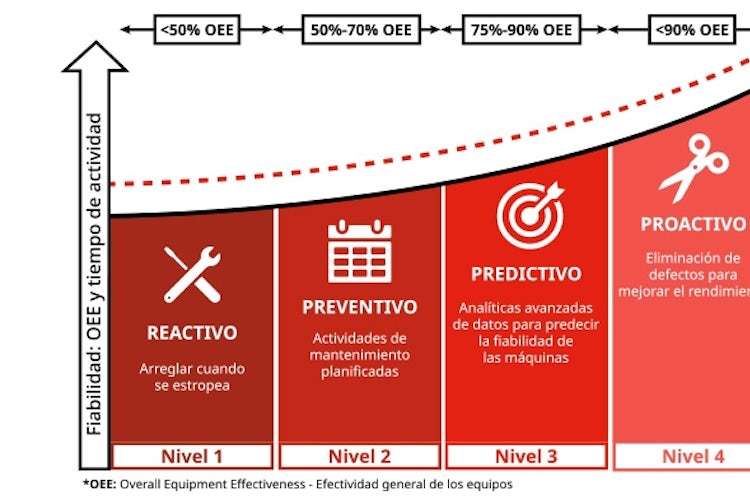
En Interflon ofrecemos el programa IPM (Interflon Predictive Maintenance), este consiste en el uso de tecnología de vanguardia para identificar y prevenir averías en la maquinaria antes de que se produzcan, permitiendo evitar paradas no planificadas en la producción y sus costes asociados.
Dentro de este programa, ofrecemos diferentes técnicas de mantenimiento predictivo, como los ultrasonidos, el análisis de aceite y las termografías, con el objetivo de ayudar a nuestros clientes a descubrir cuál es el lubricante más idóneo y las frecuencias de lubricación más adecuadas para cada aplicación, garantizando la máxima productividad.
Nuestro equipo de expertos en lubricación utiliza cámaras termográficas de última generación para medir la temperatura de los componentes de tu maquinaria. Si se detectan problemas en la lubricación, ofrecemos soluciones personalizadas para eliminar cualquier problema que pueda afectar negativamente al rendimiento de la máquina.
En conclusión, el servicio IPM proporciona multitud de ventajas:
⏱️ 1.Detección temprana de problemas de lubricación.
🛠️ 2.Evitar paradas no planificadas.
💶 3.Reducir costes de mantenimiento.
⚙️ 4.Prolongar la durabilidad de los equipos.
💡 5.Mejorar la eficiencia energética.
⛑️ 6.Mejorar la seguridad laboral.
✔️ 7.Facilitar la toma de decisiones.
🕵️♂️ 8.Ahorrar tiempo en inspecciones manuales.
🔧 9.Prevenir fallos y roturas.
Mantener los rodamientos en buen estado, no sólo requiere el uso de tecnología como la de ultrasonidos, sino que también es imprescindible utilizar un lubricante con la calidad y las características más adecuadas para cada aplicación. En Interflon disponemos de una amplia gama de grasas para todas las necesidades.
En Interflon ofrecemos el servicio de ultrasonidos como parte de nuestro programa IPM. Mediante este, nuestro especialista realiza una auditoría o monitoreo de la lubricación en los rodamientos (especialmente aquellos de alto coste o más críticos) para determinar el producto y las frecuencias más adecuadas.
Gracias a la tecnología ultrasónica, se pasa del mantenimiento correctivo al predictivo, se garantiza un re-engrase perfecto y el máximo rendimiento, utilizando la grasa correcta, el programa de engrase correcto y la cantidad correcta, evitando los dos errores más comunes en la lubricación de rodamientos:
- Lubricación en base a tiempo: sin considerar todos los factores que influyen al elegir la grasa para un rodamiento.
- El sobre y bajo engrase: utilizar demasiada grasa, o por contrario no utilizar suficiente. Ambas acciones conducen al desgaste, deterioro o la rotura permanente de los rodamientos, generando daños graves a la maquinaria. Haz clic para más información.
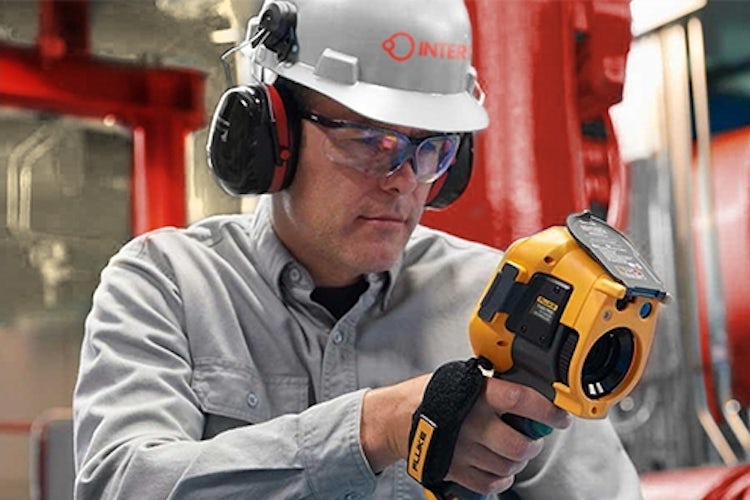
Termografías
Las termografías son una herramienta fundamental para el mantenimiento preventivo de la maquinaria. Esta técnica permite detectar con antelación posibles fallos en los equipos, mediante la medición y visualización de la distribución de temperatura en las superficies de estos.
Para realizarlas se utiliza una cámara termográfica que mide y muestra la radiación infrarroja emitida por los objetos. Gracias a ello, los expertos pueden analizar las imágenes obtenidas para detectar posibles anomalías en la distribución de temperatura, lo que puede ser un indicador de problemas en la lubricación. Así se pueden prevenir paradas no planificadas y prolongar la vida útil de los equipos.
⏰ 1.Detección temprana de problemas
Detección temprana de anomalías en la temperatura de los equipos. Estas irregularidades son indicadores que reflejan la falta de lubricación o la contaminación del lubricante, pudiendo tomar medidas preventivas para evitar fallos más graves que pongan en riesgo a la maquinaria y a los operarios de mantenimiento.
💶 2.Ahorro de costes, tiempo y recursos
Identificación rápida de las máquinas que requieren más atención para enfocar los esfuerzos en estas y desarrollar planes de mantenimiento preventivo. Técnica no intrusiva con la que no es necesario desmontar las máquinas o interrumpir la producción para realizar inspecciones, ahorrando en tiempo y mano de obra.
⚙️ 3.Optimización del mantenimiento
Optimización del mantenimiento, pasando del mantenimiento correctivo al predictivo, evitando fallos graves y paradas de producción no programadas. Además, una lubricación adecuada mejora la eficiencia de los equipos y reduce el consumo energético, mejorando la vida útil de la maquinaria.
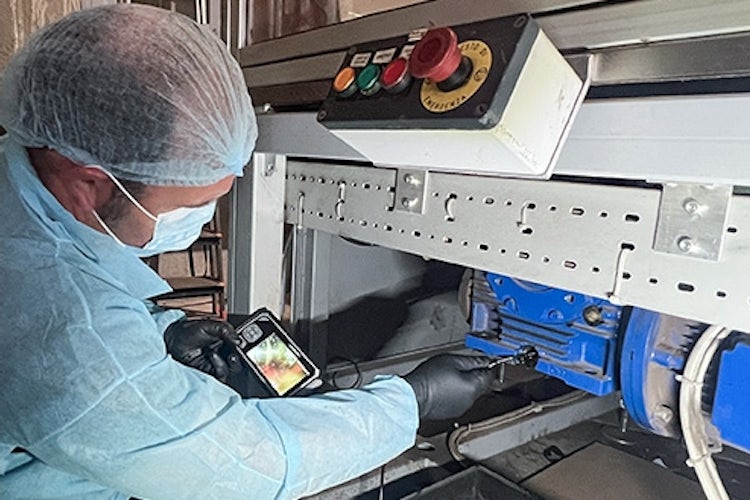
Endoscopia industrial
La endoscopia industrial permite explorar zonas inaccesibles o del interior de los equipos, obteniendo imágenes precisas que permiten realizar un análisis exhaustivo de los componentes inspeccionados sin necesidad de desmontar la maquinaria. Para ello, se utiliza una cámara endoscópica o boroscopio, un instrumento que consiste en una micro cámara que se puede introducir por pequeños conductos o huecos de tamaño reducido, con el fin de inspeccionarlos y ver las imágenes en la pantalla.
Beneficios de las endoscopias industriales
Implementar las endoscopias industriales te ofrecerá diferentes ventajas:
1. Acceso visual interno: visión directa y detallada del interior de los componentes sin necesidad de desmontarlos.
2. Detección de problemas ocultos: revelar problemas internos que no son visibles a simple vista, como el desgaste, fugas, etc.
3. Ahorro de tiempo y recursos: al no desmontar los componentes se reducen los tiempos de inspección y se evitan desmontajes.
4. Mejora de la seguridad: al no requerir desmontar los equipos, se reduce el riesgo de accidentes laborales y lesiones asociadas.
5. Documentación y seguimiento: las imágenes capturadas se pueden documentar para realizar un seguimiento y comparativa.
6. Aumento de la vida útil de los equipos: al realizar inspecciones endoscópicas se mantienen los equipos en condiciones óptimas más tiempo, reduciendo los fallos y mejorando la eficiencia.
GBE Analysis
Con GBE Analysis, nuestros técnicos especializados realizarán por ti las endoscopias industriales, documentando todo el proceso para garantizar buenos resultados y acompañándote en todo el proceso.
Realizaremos un análisis exhaustivo del interior de tus reductores y cajas de engranajes para determinar si se encuentran en buen estado, detectar si es necesario realizar un análisis de aceite para detectar partículas metálicas, si hay que realizar un cambio de aceite a grasa líquida, entre otros aspectos cruciales para garantizar un buen mantenimiento.
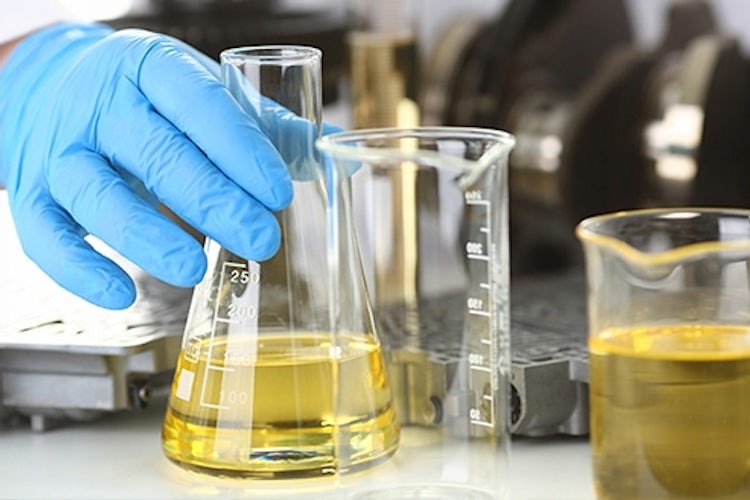
Análisis de lubricantes
¿Sabías que el estado de tus aceites y grasas lubricantes puede afectar al rendimiento de tu maquinaria? Las paradas no planificadas en la producción industrial suponen un coste medio de 50.000 millones de euros al año por sector y se deben en gran medida por no implementar el mantenimiento preventivo o predictivo.
En cualquier proceso de producción es vital mantener la maquinaria en buen estado, ya que cualquier fallo puede provocar paradas imprevistas que retrasan los plazos de entrega y que pueden afectar a la rentabilidad de la empresa. Además, la mayoría de fallos de la maquinaria que resultan en paradas, se pueden evitar mediante el análisis de lubricantes y una correcta lubricación con el producto más idóneo.
El análisis de lubricantes consiste en evaluar la calidad del lubricante utilizado en la maquinaria, para determinar si es necesario realizar algún cambio o mantenimiento preventivo. Estos análisis permiten detectar e identificar futuros fallos de la maquinaria hasta 6 meses antes de que se produzcan, así como evaluar si el lubricante está en condiciones óptimas o detectar cuando realizar un cambio de lubricante, etc.
En resumen, al analizar los lubricantes se obtienen varios beneficios:
🔎 1.Identificación y prevención de problemas.
El análisis de lubricantes puede detectar problemas en los componentes de la maquinaria antes de que se conviertan en fallos graves. Esto permite que se tomen medidas preventivas antes de que se produzcan daños importantes en la maquinaria, lo que puede ahorrar tiempo y costes de reparación significativos.
📉 2.Reducción de costes.
El análisis de lubricantes puede ayudar a identificar la necesidad de cambiar el lubricante o los correctos intervalos de lubricación, lo que puede reducir los costes de mantenimiento y lubricación, así como la cantidad de residuos producidos.
📈 3.Incremento de la eficiencia.
Al mantener los lubricantes en buen estado, se reduce la fricción y el desgaste, lo que puede aumentar la eficiencia y prolongar la vida útil de la maquinaria. Además, se pueden realizar ajustes precisos en la viscosidad y propiedades del lubricante a aplicar, contribuyendo a la optimización del rendimiento.
🦺 4.Mayor seguridad en el lugar de trabajo.
Al detectar los problemas de forma anticipada, el análisis de lubricantes puede ayudar a prevenir accidentes y reducir el riesgo de lesiones en el puesto de trabajo.
📋 5.Cumplimiento normativo.
El análisis de lubricantes puede ayudar a asegurar el cumplimiento de las regulaciones ambientales y de seguridad aplicables, lo que puede evitar sanciones y multas.
📆 6.Mejora de gestión y planificación.
En análisis de lubricantes proporciona información útil sobre el estado de la maquinaria, lo que puede ayudar a programa y planificar el mantenimiento de manera más eficiente y efectiva, además de contribuir a la toma de decisiones sobre la inversión en nueva maquinaria.

En Interflon trabajamos junto a un laboratorio especializado para ofrecer el servicio de análisis de aceites y/o grasas. Este servicio está diseñado para ayudar a nuestros clientes a mantener la maquinaria siempre en condiciones óptimas, evitando elevados costes de reparaciones y de paradas productivas.
Proporcionamos un servicio de alta calidad, realizando la recogida y proporcionando las muestras al laboratorio para analizar el aceite y/o grasa. También proporcionamos informes personalizados, detallando los puntos clave de los resultados del informe de laboratorio, junto a una conclusión de los resultados y recomendaciones precisas para garantizar la eficiencia de la maquinaria.
Con Interflon Predictive Maintenance, puedes confiar en que tus equipos estarán en las mejores manos. Nuestro enfoque proactivo y orientado a resultados te ayudará a minimizar los tiempos de inactividad, reducir los costos de mantenimiento y maximizar la productividad de tu planta.
¡No te arriesgues con el mantenimiento reactivo! Descubre cómo Interflon IPM puede transformar tus operaciones. Contáctanos hoy mismo y permítenos llevar tus equipos al siguiente nivel de rendimiento y eficiencia.