Aligning reliability and sustainability through innovation in lubrication technologies
Reframing Technical Maintenance
The manufacturing industry is a capital intensive sector with a significant CO2 footprint. The Paris Climate Agreement’s objective for net-zero CO2 emissions shortly after mid-century completely transforms the industrial manufacturing agenda and will drive a significant part of the capital allocation going forward. Although modifications and end-of-life asset replacements are the best opportunity for significantly reducing CO2 emissions a more basic approach for short term success should (and could) be considered.
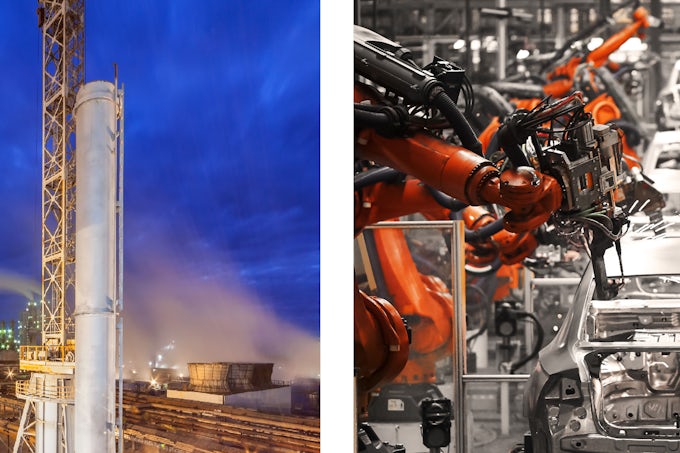
In total 20% (103 EJ) of the world’s total energy consumption is used to overcome friction. Implementing advanced tribological technologies can reduce the CO2 emissions globally by as much as 1,460 MtCO2 and result in 450,000 million Euros cost savings in the short term. In the longer term, the reduction can be 3,140 MtCO2 and the cost savings 970,000 million Euros [1].
By taking advantage of the new surface, materials, and lubrication technologies for friction reduction and wear protection in machinery and other equipment worldwide, energy losses due to friction and wear could potentially be reduced by 25% in the long term (15 years) and by 10% in the short term (8 years) [1].
Investments in new surface and materials technologies is predominantly a long term, end-of-life, asset replacement decision and part of a capital expenditure (CAPEX) business case and subsequently investment strategy. Short term gains are made by evaluating lubrication technologies that are designed specifically for significant friction reduction and wear protection. These cases can, and should, be substantiated by a business case that demonstrates a CO2 emission reduction while also reducing total cost of ownership (TCO).
Poor lubrication accounts for over 36% of premature bearing failures and has the potential to negatively impact the maintenance budget by as much as 40% due to excessive (un)planned maintenance and below designed mean time between failure (MTBF) [2]. Friction in general and premature failures in particular have the potential to negatively impact the performance and reliability of the manufacturing industry resulting in low overall equipment effectiveness (OEE), low operating profit and low return on capital employed.
Selecting lubrication technologies that are designed specifically for friction reduction and wear protection should be high on the agenda of every manufacturing executive, it will contribute to CO2 emission goals while reducing total cost of ownership hence improving shareholder value.
[1] Holmberg K, Erdemir A. Influence of tribology on global energy consumption, costs and emissions: 263-284 (2017)
[2] SKF