Lubricating conveyor chains at free-range laying company Larei
Food safe lubricants
These chickens are not chained!
No fewer than 120.000 chickens lay an average of 110.000 eggs a day at Larei free-range laying company in Zeewolde. The two passionate owners, the Roos-couple, have a maximum focus on sustainability and the welfare of their animals. Because of that reason they chose for food-grade lubricants from Interflon for lubrication of different conveyor chains for eggs, feed and manure.
'If you take good care of your animals, the animals will take good care of you', is the motto of Daniëla Roos-Lambregtse and Mark Roos. For these reasons, the chickens of these entrepreneurs can roam around both indoors and outdoors (in a covered winter garden). The company invests in sustainability in various areas: various PV panels generate the electricity on the chicken manure using a dryer that is converted into fuel. The dryer uses the stable air heated by the chickens for the drying process.
Automation
With 110.000 eggs collected by hand every day, the company cannot escape a bit of automation. The logistics processes are technically supported, which starts with the laying nests: they roll on a conveyor belt via an oblique side, which changes into a conveyor chain: the bar belt. They are then processed by a so-called egg packer and placed on pallets by a robot.
Lubrication of chains
It is relatively dusty around the habitat of the chickens, which means that, among other things, the bars for the eggs are hard to handle, has to last. "I've always only lubricated this chain minimally," says Mark Roos. “You don't want any lubricant to get on the eggs and eliminate the risk of dioxin. But in the meantime you have to lubricate, otherwise things will come to a standstill.' In the end, this is what happened. Due to a lack of lubrication, the rollers in the chain broke, which was a sign for Mark to look for suitable lubricants: an oil that lubricates sufficiently, is harmless with regard to dioxin and is safe for the environment and food. This issue was not a problem for Interflon. From the wide range of food-grade lubricants, Interflon Food Lube aerosol was chosen. Mark Roos: 'After applying this oil, the problems were really solved. The chain now runs properly and is also much quieter. Moreover, the food-grade oil cannot harm our eggs and chickens.”
Around the table
The solution for this conveyor chain was the immediate reason to look further in the company for points where the lubrication could be improved. As a result of this inspection round, the lubricating grease for the open teeth was, among other things, wheels of the feed chains have been replaced by a food-grade variant: Interflon Food Grease MP2.
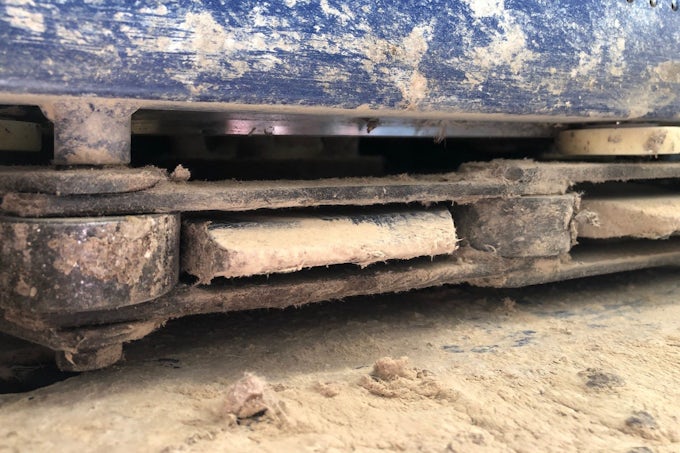
The chains combined with the manure dryer were a bigger challenge. These run in a very dusty environment (chicken dust that comes with the air), causing the chains to crack. Mark: 'We had previously inquired about a solution from the supplier of the chains. He advised us to install an automatic lubrication system, which would amount to € 6.400,- per dryer. We would also need compressed air, which would amount to an extra € 5.000,- for compressor and pipes. These investments were beyond our budget and I also didn't like a compressed air system in a dusty room.
Interflon proposed an automatic lubrication system with Interflon Lube PN68 which is now installed and running. Mark: “Without cracking. The chains remain nice and dry on the outside, so that they don't attract dust and dirt, while the rollers remain nicely greased on the inside. I don't have to do anything about it myself. When the system indicates that the oil is about to run out, we top up the system. But that's about it.”
Perfect example of a positive business case
The above measure has saved Larei the necessary costs:


Advice
The arrival of Interflon has strengthened the importance of good lubrication at the company. “Interflon not only supplies lubricants, but also knowledge,” says Mark. ‘For example, the bearings of a return roller broke too often in our opinion. As far as we're concerned, it couldn't be the lubrication, because the bearing was well-greased. Sufficient lubricant you would think. After an inspection by Interflon, we were advised to use less lubrication. Instead of two pinches, we now apply one pinch and that indeed solved the problem. You just have to know.”
Thanks to the collaboration with Interflon and the open and inquisitive attitude of the Roos family, the lubrication maintenance at Larei has been lifted to a higher level. ‘By now lubricating in the right way with the right agents, I prevent downtime, I reduce maintenance costs and, moreover, do not consume unnecessary energy as a result of friction. 'I have earned back the costs in no time' concludes Roos.