Beneficios que van más allá del ahorro
Incluso un buen mantenimiento de lubricación puede mejorarse
En las últimas dos décadas, el mantenimiento de lubricación ha pasado de ser una tarea delegada a un técnico junior a convertirse en una disciplina científica. Esta transformación se debe a los avances en la tecnología de lubricantes, al crecimiento del conocimiento técnico y a la disponibilidad de herramientas avanzadas de monitoreo y análisis. Peter Bakkum, Director General de Interflon Holanda, ha dedicado años a difundir buenas prácticas de lubricación.
“Lo notable es que incluso empresas que aparentemente ‘lo hacen bien’ —con pocas o ninguna avería— suelen tener un margen de mejora considerable. En esos casos, el beneficio no está solo en evitar fallas, sino también en liberar ahorros ocultos.” Peter Bakkum
La base de una lubricación eficaz
Bakkum explica que la lubricación de máquinas cumple tres funciones clave: reducir la fricción entre partes móviles, disipar calor y proteger las superficies. “Para lograr esto de manera eficaz, se necesitan los lubricantes adecuados, aplicados en el momento correcto, en la cantidad justa y de la forma correcta. La mayoría de las empresas tiene oportunidades de mejora en todos estos aspectos, aunque muchas veces no lo saben.”
El impacto de una lubricación correcta
Las empresas que cumplen con todos los requisitos de un mantenimiento de lubricación efectivo obtienen beneficios en varias áreas, con el consecuente ahorro de costos. La eficiencia energética es uno de los ejemplos más claros. “Investigaciones globales indican que aproximadamente el 20% del consumo energético mundial se destina a vencer la fricción”, señala Bakkum. “A partir de eso, es fácil calcular lo que esto implica en consumo de energía, costos asociados y huella de CO₂. Aunque estas cifras no son nuevas, muchos aún no son conscientes de que una lubricación adecuada puede contribuir de forma significativa a reducir la fricción y mejorar la eficiencia energética.”
Además, un buen mantenimiento de lubricación prolonga la vida útil de los equipos. Componentes bien lubricados y con mínima fricción se desgastan menos y fallan más tarde en su ciclo de vida. “Y si eso lo traducimos a costos, diversos estudios muestran que entre el 15% y el 40% de los gastos de mantenimiento se deben a una lubricación incorrecta.”
A esto se suma la posibilidad de reducir considerablemente los costos de mantenimiento. Y gracias a los avances constantes, las oportunidades de mejora no dejan de crecer.
Avances en conocimiento y tecnología de lubricación
Bakkum destaca el conocimiento desarrollado en los últimos años en áreas como tribología, formulación de lubricantes, aditivos y determinación de cantidad y frecuencia óptima de aplicación. Pero llevar ese conocimiento a la práctica sigue siendo un reto.
“Los fabricantes y proveedores de lubricantes comparten esa información”, explica, “pero su impacto en la realidad aún es limitado. Mucha energía se sigue perdiendo por fricción excesiva. Componentes agarrotados, rodamientos que fallan antes de tiempo por falta de lubricación y temperaturas de operación elevadas siguen siendo demasiado comunes. No suele ser por negligencia, sino por falta de conocimiento práctico sobre lubricación, un conocimiento que es esencial para una aplicación eficaz y eficiente.”
En la práctica, el personal de mantenimiento rara vez recibe una formación en profundidad sobre cómo funcionan los lubricantes, qué hacen y cómo aplicarlos correctamente. “Si no está claro qué lubricante usar, cómo aplicarlo o si un punto de lubricación es de difícil acceso o no está bien calendarizado, el riesgo de que se omita sin querer es alto”, advierte Bakkum.
Una cuestión también de gestión
También existen barreras a nivel de gestión. “Desde una lógica de costos, es comprensible que la lubricación se perciba como algo secundario”, continúa Bakkum. “Pero tanto la investigación como la experiencia práctica demuestran que ahí es donde están muchas veces las mayores oportunidades: en la disponibilidad de los equipos, la reducción de costos energéticos y de mantenimiento, y la disminución de paradas no planificadas. Sin embargo, el desgaste, el recambio de componentes o las detenciones inesperadas se suelen aceptar como ‘parte del negocio’, aunque en muchos casos son evitables.”
Bakkum menciona un estudio de la Universidad de Southampton sobre pérdidas de producción provocadas por fricción, desgaste y lubricación deficiente: “Si extrapolamos esos datos a un país industrializado como los Países Bajos, la pérdida anual estimada asciende a casi 6 mil millones de euros. Esa cifra —solo en los Países Bajos— muestra el enorme valor que aún puede recuperarse mediante un mantenimiento de lubricación bien estructurado.”
Es momento de un nuevo enfoque
Pero volvamos al motivo de este artículo: también existe un grupo de empresas que prácticamente no presentan fallas vinculadas a la lubricación, y aun así tienen un amplio margen de mejora.
“Puede sonar contradictorio”, explica Bakkum, “pero cuando se analiza más de cerca, muchas veces la ausencia de problemas se debe a una estrategia de mantenimiento preventivo. En estos casos, los componentes se reemplazan de forma anticipada y muchas veces demasiado pronto, sin investigar por qué realmente están fallando. En el caso de los rodamientos, la causa raíz suele estar en la lubricación, en particular en el uso de un lubricante inadecuado. Y eso no siempre se debe a una mala elección inicial. Con el tiempo, las máquinas se exigen más y pueden operar fuera de los límites de temperatura o presión de ciertos lubricantes. En esos casos, la necesidad de ajustar el lubricante pasa desapercibida —lo cual, siendo justos, es comprensible.”
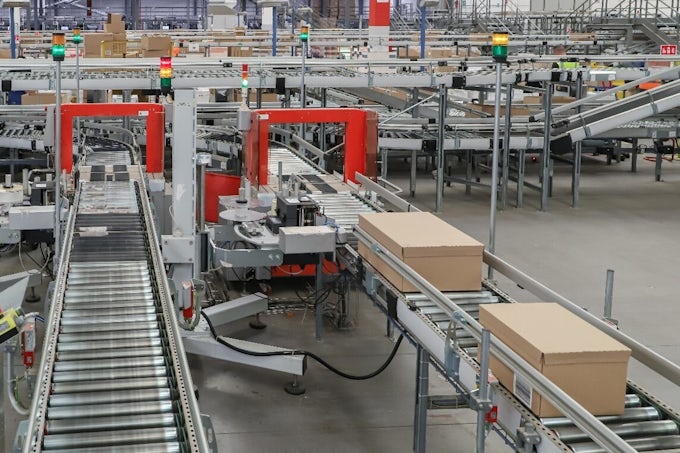
Un enfoque integral
Para las empresas que buscan reestructurar su mantenimiento de lubricación, revisar su enfoque actual o avanzar hacia una estrategia profesional, Interflon propone una hoja de ruta práctica paso a paso:
- Auditoría integral: identificar todos los puntos de lubricación, propiedades relevantes de las máquinas, lubricantes actuales y frecuencias de mantenimiento.
- Revisión de compatibilidad: verificar que los lubricantes actuales sigan siendo adecuados para los equipos, considerando posibles cambios en velocidades, presiones o condiciones del entorno.
- Optimización de productos: trabajar con especialistas para asegurar el lubricante adecuado para cada aplicación y reducir la variedad de productos utilizados. “Este paso es donde más valor aporta la intervención de un especialista”, indica Bakkum. “Pueden evaluar la idoneidad de los lubricantes y ayudar a reducir la cantidad de productos en uso, que suele aumentar con nuevas adquisiciones o cambios de personal. Esto reduce costos logísticos y minimiza el riesgo de errores.”
- Optimización de frecuencias: determinar los intervalos de lubricación adecuados con asesoramiento técnico.
- Soluciones avanzadas: considerar medidas adicionales para reducir aún más costos, como:
• Sistemas automáticos de lubricación que cubren múltiples puntos, reducen costos, ahorran lubricante y garantizan la aplicación en tiempo y forma.
• Integración con programas de mantenimiento existentes para generar órdenes de trabajo automáticas y construir datos históricos que permitan análisis de tendencias y optimización
“Estas herramientas pueden adaptarse al nivel de ambición de cada empresa”, concluye Bakkum. “Se puede empezar con acciones rápidas, enfocarse en equipos críticos o resolver casos puntuales. Una vez que los beneficios se hacen visibles y se gana apoyo interno, la expansión del enfoque se vuelve un paso natural.”
¿Quiere saber cómo optimizar tu programa de mantenimiento de lubricación y qué impacto puede tener en tu operación?
Contácteses con los especialistas de Interflon para identificar oportunidades ocultas, reducir costos y mejorar el rendimiento de tus equipos con una estrategia adaptada y resultados medibles.
Este artículo fue escrito por la ingeniera M. de Wit - Blok. Fue publicado en la revista Vakblad Aandrijftechniek el 11 de abril de 2025 y ha sido traducido del neerlandés.