The value of MicPol® technologie
100% saving on bearing spare parts of a double winches
Old situation
Due to the influence of dirt, moisture and salt, the bearings wear out faster than normal and will eventually fail. Every hour the winch of the crane is idle costs money instead of making money. And because there is often a long delivery time on parts, the costs increase further without the job being done. The crane in this example has about 600 running hours and trends show that these will continue to increase. As a result, failure of these bearings will have a relatively increasing impact on uptime and ultimately ROI.
Solution
After extensive testing, Interflon Grease LS 1/2 with MicPol Technology was selected as the preferred grease for the swing bearing. The grease's high performance reduces consumption by a factor of 4. This results in lower costs, less CO2 emissions and less risk of breakdowns.
Results(after 4 years):
• 85% lower cost
• 100% saving on spare parts
• No downtime
• 72% less grease consumption
• 23% less CO2 ouput on lubricants (-1.202 kg/CO2)
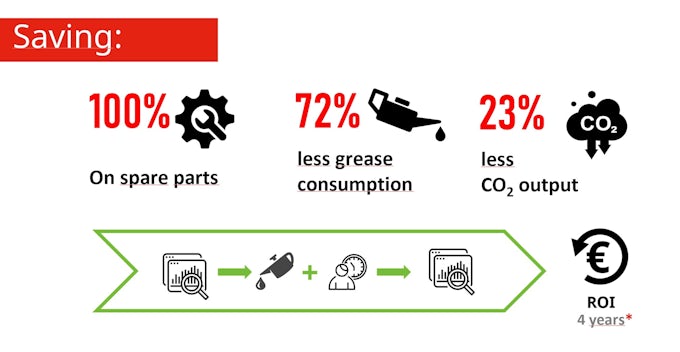
*Note:
The exact costs of downtime are not known so they could not be included in the calculation. Therefore, this example only shows the savings on the two bearings. If the costs of downtime could have been included, the calculation would clearly show that the actual savings are many times higher.