Identifica los errores de lubricación más comunes y aprende cómo evitarlos para mejorar la fiabilidad, eficiencia y vida útil de tus equipos industriales.
10 errores de lubricación que causan las principales averías
Los lubricantes desempeñan un papel muy importante en el funcionamiento eficiente de las máquinas, pues su misión principal es reducir la fricción y el desgaste de las superficies en contacto de componentes mecánicos en movimiento.
Una lubricación incorrecta es la causa más común de los problemas mecánicos, de hecho, una investigación realizada por el Instituto de Tecnología de Massachusetts concluyó que el 70% de las averías mecánicas se deben a errores de lubricación.
La lubricación deficiente, la aplicación incorrecta o el mantenimiento inadecuado de los sistemas de lubricación no son suficientes para enfrentar los desafíos que presentan las condiciones extremas de temperatura, la corrosión o la contaminación, a los que a menudo están expuestos los equipos industriales.
Estas problemáticas derivadas de una lubricación inadecuada pueden provocar graves consecuencias debido al desgaste acelerado de los componentes mecánicos de la maquinaria:
- El aumento del consumo energético.
- Averías que obligan a realizar paradas de producción no planificadas.
- Riesgos de seguridad.
Ante estas incidencias que comportan altos costes en mantenimiento correctivo es necesario tener presentes los principales problemas de lubricación.

Principales errores en la lubricación industrial
1. Uso de lubricante inadecuado:
Elegir un lubricante que no sea adecuado para las condiciones operativas, como temperatura, presión, contaminación o tipo de material, tiene como consecuencias el desgaste excesivo, la mala protección contra la fricción y el calor, así como los fallos prematuros en los componentes.
2. Contaminación del lubricante:
El lubricante puede contaminarse con polvo, agua, partículas metálicas, productos químicos y otras sustancias, lo que puede provocar abrasión, corrosión, formación de lodos y una pérdida significativa de su capacidad lubricante. Estos efectos aceleran el desgaste, lo que a su vez puede causar fallos graves en rodamientos, engranajes u otros componentes críticos.
3. Defecto o exceso de cantidad de lubricante:
Aplicar una cantidad insuficiente de lubricante o sufrir fugas que reduzcan su nivel, genera desgaste entre las superficies de contacto y aumenta la fricción, provocando daños por fricción y fallos mecánicos prematuros. Por otro lado, aplicar demasiado lubricante, ya sea por sobrecarga o errores de mantenimiento, puede causar un aumento de la temperatura, fugas y una mayor acumulación de contaminantes.
4. Lubricante degradado o envejecido:
Los lubricantes pierden sus propiedades con el tiempo debido a la oxidación, contaminación o exposición a condiciones extremas. Ante estas condiciones, se forma una película de lubricación menos efectiva, lo que aumenta el desgaste y la fricción. También se pueden formar depósitos sólidos o lodos que obstruyen el sistema de lubricación perdiendo la funcionalidad del lubricante.
5. Incompatibilidad de lubricantes:
Mezclar diferentes tipos de lubricantes (por ejemplo, base mineral y sintética) puede causar reacciones químicas adversas. Ello supone: una pérdida de viscosidad, formación de espuma, depósitos sólidos o pérdida de propiedades protectoras, lo que compromete la lubricación efectiva.
6. Fallo en los sistemas automáticos de lubricación:
Fallos en los sistemas automáticos de lubricación (como bombas, inyectores o sistemas de lubricación centralizados) provocan que el suministro de lubricante puede interrumpirse o ser inconsistente, lo que puede provocar un rápido desgaste de los componentes.
7. Inadecuada aplicación del lubricante:
Errores en la aplicación del lubricante, como usar herramientas sucias, aplicar en lugares incorrectos o en cantidades incorrectas, puede comprometer la lubricación efectiva.
8. Condiciones de operación fuera de los límites especificados:
Cuando la maquinaria trabaja en condiciones extremas, como temperaturas muy altas o bajas, o bajo cargas superiores a las diseñadas para la máquina, sin ajustar la lubricación, hace perder efectividad del lubricante.
9. Pérdida de viscosidad del lubricante:
La viscosidad del lubricante puede cambiar debido a la temperatura o degradación. Una viscosidad inadecuada puede generar una película lubricante demasiado delgada o espesa, lo que no protegerá adecuadamente las superficies de fricción.
10. Corrosión por lubricantes:
Algunos lubricantes contienen aditivos que pueden ser corrosivos si no son compatibles con los materiales del sistema y componentes del equipo. La corrosión de las piezas metálicas, por la formación de óxidos, supone la degradación acelerada de los componente
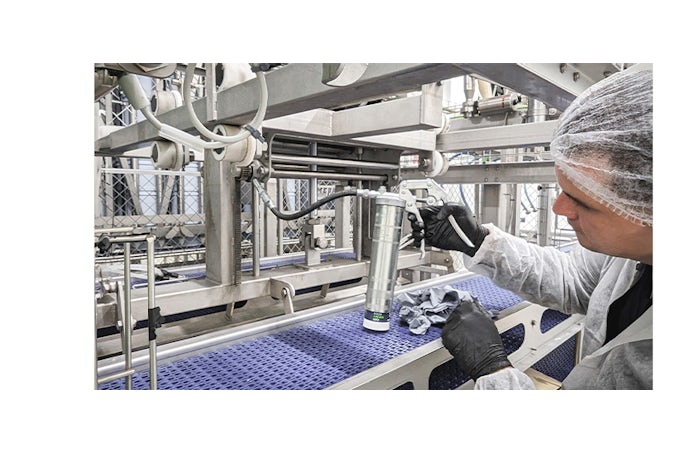
Cómo evitar los errores en la lubricación industrial
Para abordar los errores mencionados, es fundamental adoptar un enfoque integral que contemple diversos aspectos de la gestión del lubricante. Primero, es esencial realizar un análisis exhaustivo de las condiciones operativas específicas de cada máquina, lo que incluye evaluar factores como temperatura, presión, tipo de material y el entorno en el que opera el equipo. Esta evaluación debe guiar la selección del lubricante adecuado, que no solo cumpla con las especificaciones del fabricante, sino que también haya sido probado en condiciones similares a las de operación para garantizar su eficacia.
La implementación de un programa de mantenimiento preventivo es crucial para evitar problemas relacionados con la calidad y cantidad del lubricante. Esto incluye auditorías periódicas que evalúen la integridad del lubricante, así como revisiones regulares de los sistemas automáticos de lubricación. Para asegurar una aplicación precisa y adecuada, se deben utilizar sistemas de medición y control que minimicen el riesgo de error humano y garanticen que la cantidad de lubricante aplicada sea la correcta. La capacitación del personal en prácticas adecuadas de lubricación y el uso de herramientas limpias también son vitales para evitar la contaminación del lubricante, que puede surgir de la introducción de partículas extrañas o productos químicos.
Es importante prestar especial atención a las condiciones operativas. Si las máquinas operan en entornos que superan los límites recomendados, se deben ajustar las prácticas de lubricación, lo que puede incluir la selección de lubricantes de mayor rendimiento o el incremento de la frecuencia de lubricación. Además, el monitoreo continuo de la temperatura y la viscosidad del lubricante permitirá detectar cambios que podrían comprometer la protección de las superficies de fricción.
Por último, es esencial elegir lubricantes compatibles con los materiales del equipo para prevenir reacciones químicas adversas que puedan resultar en corrosión. Mantener buenas prácticas de mantenimiento, que incluyan la limpieza regular de las superficies de contacto y la revisión de los lubricantes antes de su aplicación, es clave para asegurar un rendimiento óptimo y prolongar la vida útil de los componentes.
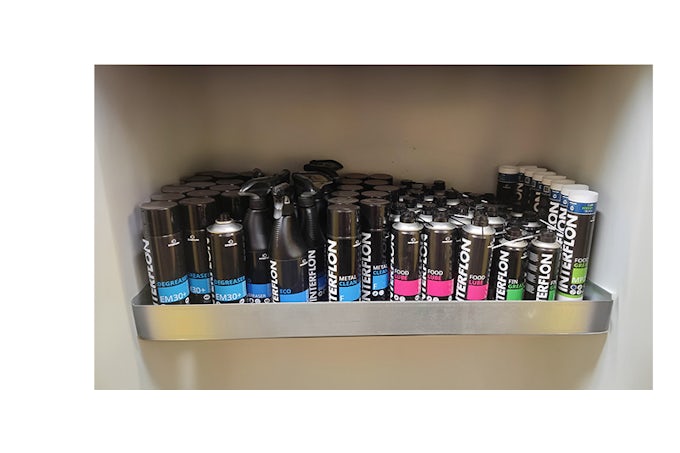
En resumen, solucionar estos problemas implica un adecuado mantenimiento, selección y monitoreo de los lubricantes, asegurando que las condiciones operativas sean las correctas para cada tipo de sistema de lubricación. Una correcta lubricación es esencial para proteger los equipos mecánicos, aumentar su vida útil, mejorar la eficiencia energética y reducir costos de mantenimiento, pues, así se garantiza el funcionamiento continuo y fiable de las máquinas.
Si quieres asegurar la máxima eficiencia de tus operaciones y minimizar el riesgo de averías, le invitamos a conocer nuestro plan de lubricación Double MP. Nuestro enfoque integral no solo incluye el análisis de sus necesidades específicas y la selección de lubricantes óptimos, sino también auditorías frecuentes y capacitación del personal para implementar prácticas de lubricación efectivas. Contacta hoy y da el primer paso hacia un mantenimiento más eficiente y seguro de sus equipos.
Solicita asesoramiento técnico especializado
🔍 ¿Buscas mejorar la fiabilidad de tus equipos, reducir averías o seleccionar el lubricante más adecuado para tus condiciones operativas?
Nuestro equipo de expertos en lubricación te ayudará a identificar la solución óptima para tus aplicaciones, con productos que maximizan el rendimiento y reducen los costes operativos.
📩 Rellena el formulario de contacto y recibe una propuesta técnica adaptada a las necesidades de tu planta o maquinaria.