Insight into lubrication film types reduces wear, lowers costs and improves reliability
Lubrication regimes explained: from boundary to full-film, and why it matters
Unplanned downtime, high energy bills, and early bearing failures, often, the root cause lies in something as basic as inadequate lubrication practices. Understanding how lubrication films behave under different conditions is key to solving these issues and optimising machine performance.
Lubrication is the process of reducing friction and wear by introducing a lubricant between two moving surfaces. An effective lubrication film prevents direct metal-to-metal contact and protects against damage, heat build-up and premature failure.
In addition to reducing friction, proper lubrication contributes to:
• Heat dissipation
• Noise reduction
• Corrosion protection
• Sealing performance
• Removal of contaminants
The condition of the lubrication film largely determines the level of protection and is influenced by factors such as speed, load, temperature and viscosity. Lubricants with MicPol® technology contain micronized particles to fill surface asperities and polarize them so they bond into an ultra-thin, durable protective layer that minimizes friction by shielding contacting surfaces. This friction reduction decreases wear, extends service intervals, lowers energy consumption, reduces downtime, improves heat dissipation, quiets operation, enhances corrosion resistance and optimizes sealing performance under all conditions.
1. Boundary lubrication
Boundary lubrication occurs at low speeds, high loads, frequent start-stop cycles or during temperature fluctuations. In this regime, the lubricant film is extremely thin or even non-continuous. Direct metal-to-metal contact is unavoidable, and the load is mainly carried by the rough surface peaks, known as asperities*.
* Asperities: microscopic surface irregularities that exist even on seemingly smooth materials.
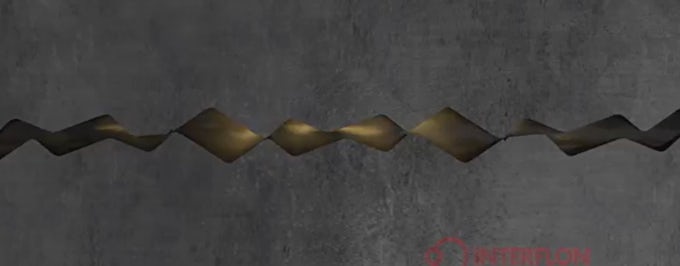
Characteristics:
• Maximum metal to metal contact
• Little to no lubricant film
Technical implications:
• Very high levels of friction and accelerated wear
• Risk of scuffing, adhesive wear or surface fatigue
• Excessive heat generation in the absence of a sufficient lubrication film
Maintenance approach:
• Use of high-performance lubricants with anti-wear and extreme pressure (EP) additives
• Careful selection of viscosity: thin enough for penetration, thick enough for surface protection
💡 In situations where boundary lubrication cannot be avoided, Interflon lubricants with MicPol® technology provide proven benefits by adhering to surfaces and significantly reducing friction and wear – even under high load or harsh conditions.
2. Mixed lubrication
Mixed lubrication is a transitional regime where both surface asperities and the lubrication film share the load. This condition is common under variable speeds or fluctuating loads. Friction decreases as the lubrication film thickens, progressing towards full-film lubrication.
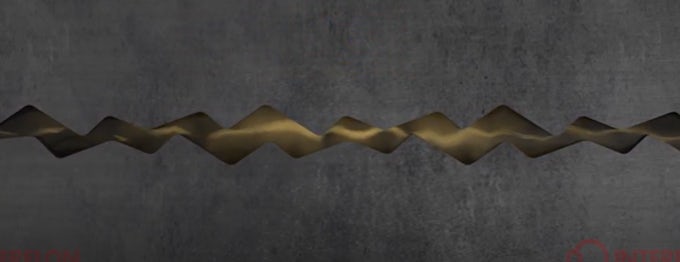
Characteristics:
• Transition stage between boundary and full-film
• No fixed ratio: load distribution shifts with speed, load and temperature
Technical implications:
• Variable friction and wear rates
• Partial surface contact, dependent on operational conditions
• Effective lubrication requires stability under dynamic conditions
Maintenance approach:
• Optimise operating conditions such as load and rotational speed where possible
• Use lubricants that maintain performance under fluctuating conditions, potentially enhanced with anchored film technologies
• Monitor vibration, temperature and acoustic signals to detect shifts between regimes
3. Full-film lubrication
In this optimal regime, the moving surfaces are fully separated by a continuous lubrication film. Friction is minimal and arises only from the internal resistance of the lubricant itself.
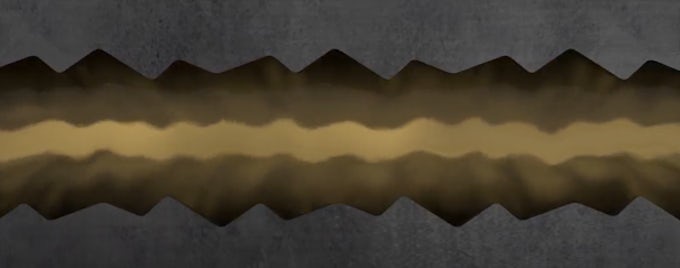
Characteristics:
• 100% load carried by lubricant
• Very high loads possible
• Surface deformation may occur under load (EHL)
• Low friction, no surface damage
Subtypes:
• Hydrodynamic lubrication – film pressure generated by relative motion (e.g. journal bearings)
• Elastohydrodynamic lubrication (EHL) – film pressure generated under high load, causing elastic deformation of the surfaces (e.g. gears, rolling element bearings)
(Optional: Hydrostatic lubrication – externally pressurised lubrication, applied when no relative movement is present)
Technical implications:
• Minimal wear and high energy efficiency
• Lubricants must maintain film integrity under pressure and temperature fluctuations
• Pressure-viscosity behaviour and elastic deformation are critical in EHL applications
Maintenance approach:
• Regular lubricant condition monitoring and viscosity analysis
• Ensure consistent and adequate lubricant supply across all load conditions
• In specific cases, solid lubricant components can further stabilise and reinforce the lubrication film
Conclusion
Effective lubrication is more than simply applying oil or grease. Each lubrication regime imposes specific demands on lubricant selection, application and maintenance strategy.
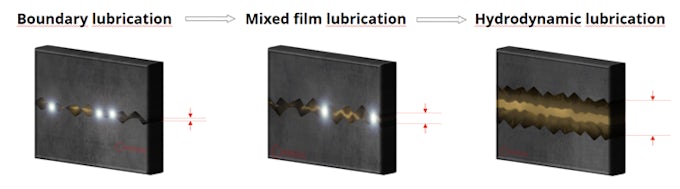
• Boundary lubrication calls for protection against direct contact to minimise wear and surface damage
• Mixed lubrication requires flexibility under changing loads and speeds
• Full-film lubrication offers optimal protection, provided the film is correctly established and maintained
Discover how our lubricants with MicPol® technology provide stable, reliable lubrication – even under challenging conditions.
Contact one of our technical advisors for a free, no-obligation consultation.